FUME EXTRACTION SYSTEM -PRODUCTS & EQUIPMENTS
INDUSTRIAL DAMPERS
PNEUMATIC DAMPERS
A pneumatic butterfly damper is a device used to block or regulate the flow of air within a duct system. It uses a butterfly valve, which is a type of valve that is similar in shape to a butterfly, to allow for the flow of air to be regulated in one direction. This is beneficial for ventilation systems, as it allows for greater control over the airflow in different areas.
How Does a Pneumatic Butterfly Damper Work?
A pneumatic butterfly damper works by using a butterfly valve to “hold back” the air, allowing it to flow in one direction while blocking or controlling the flow in the other. This device is typically connected to a tube or duct, and when the button is pressed, it opens the valve and allows air to flow through. The valve is then opened and closed by using a pneumatic actuator, which is a device that uses air pressure to create a force to move a mechanism.
Benefits of a Pneumatic Butterfly Damper
A pneumatic butterfly damper is a great way to regulate the flow of air in a ventilation system, as it allows for more precise control over the airflow. This is beneficial for cooling and heating applications, as it allows for optimal temperature control. Additionally, pneumatic butterfly dampers are designed to be very durable and reliable, making them ideal for long-term use in industrial and commercial applications.
Conclusion
A pneumatic butterfly damper is a great way to regulate the flow of air within a duct system. It allows for more precise control over the airflow, which is beneficial for cooling and heating applications. However, the mechanism is not very efficient and requires regular maintenance to ensure it is functioning properly.
MULTI LOUVER DAMPER
A pneumatic multi-louver damper is a device used to control the flow of air inside the ducting system. This device consists of a series of panels with adjustable louvers which can open or close depending on the pressure of the air passing through them. By adjusting the louvers, the amount of air passing through the ducting system can be regulated. This device is widely used in ducting of pollution control systems, HVAC (heating, ventilation, and air conditioning) industry.
Function of the Pneumatic Multi Louver Damper
The primary function of the pneumatic multi-louver damper is to control the flow of air inside the ducting system. By adjusting the louvers, the amount of air passing through the system can be regulated. This can help in maintaining a specific set point temperature as well as regulating the amount of air passing through the system. This can also be used to minimize noise levels as well as reduce the energy consumption associated with running the system.
Advantages of the Pneumatic Multi Louver Damper
One of the main advantages of the pneumatic multi-louver damper is its cost-effectiveness. This device is relatively inexpensive compared to other types of dampers. Additionally, it is relatively easy to install and maintain. The device is also relatively quiet and energy-efficient, making it a great choice for applications where energy savings are a priority.
Conclusion
The pneumatic multi-louver damper is a cost-effective and energy-efficient device used to control the flow of air inside the ducting system. This device is relatively easy to install and maintain, and can help in maintaining a specific set point temperature as well as reducing noise levels and energy consumption. However, it has its limitations and is not suitable for applications requiring high levels of air pressure.
MOTORISED DAMPER
The motorised multi louver damper is a highly innovative solution for controlling and regulating air flow in ducting systems. This device is composed of several blades, which are designed to open and close with the help of a motor. The blades can be adjusted to control the amount of air that enters the duct, allowing the user to adjust the airflow according to the desired setting.
The multi louver damper is a great option for controlling air flow, as it offers more precision than other options. It can be used in many different applications, including ventilation systems, heating systems, and cooling systems. The multi louver damper is also very reliable and will not require much maintenance.
One of the major benefits of the motorised multi louver damper is that it can be operated remotely. This allows the user to adjust the airflow without needing to enter the ducting system. This makes it much more convenient, as it eliminates the need for manual adjustment and can be operated wirelessly.
Another benefit of the motorised multilouver damper is that it is relatively quiet. This is due to the fact that it does not produce significant amounts of noise, which can be a major issue with some other types of dampers.
Finally, the motorised multilouver damper is designed to be very energy efficient. This means that it will not require a large amount of energy to operate, making it more cost effective than other types of dampers.
Overall, the motorised multi louver damper is an ideal solution for controlling air flow in ducting systems. It is reliable, can be operated remotely, and is relatively quiet and energy efficient. This makes it a great option for any application requiring precise airflow control.
POPPET DAMPER
FEC primary hoods are carefully designed based on volume of gases and furnace capacity which is provided by our clients. These hoods are manufactured in 5mm thk MS plates with stiffeners on all sides for stability. Some of side draft hoods are designed with a counterweight on another side to balance the hood moments. Kindly refer to the sample images shown.
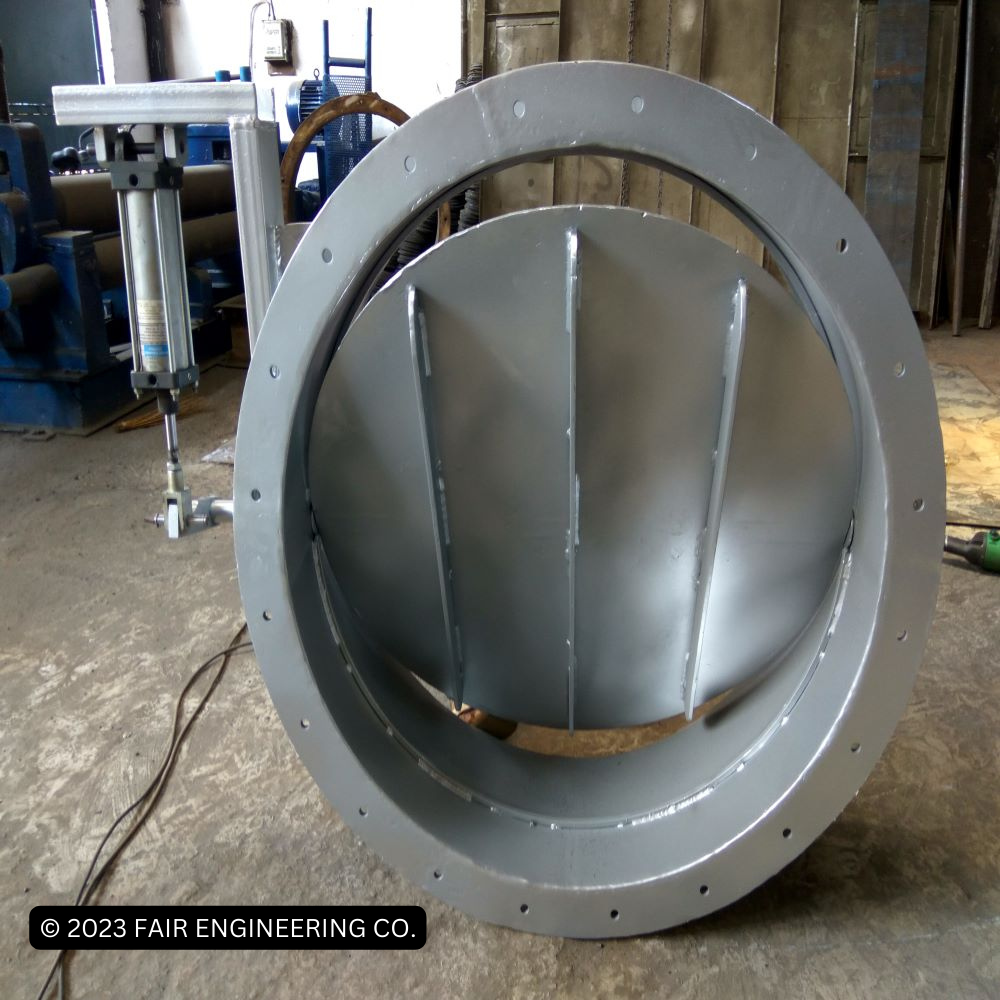
BUTTERFLY DAMPERS- PNEUMATIC TYPE
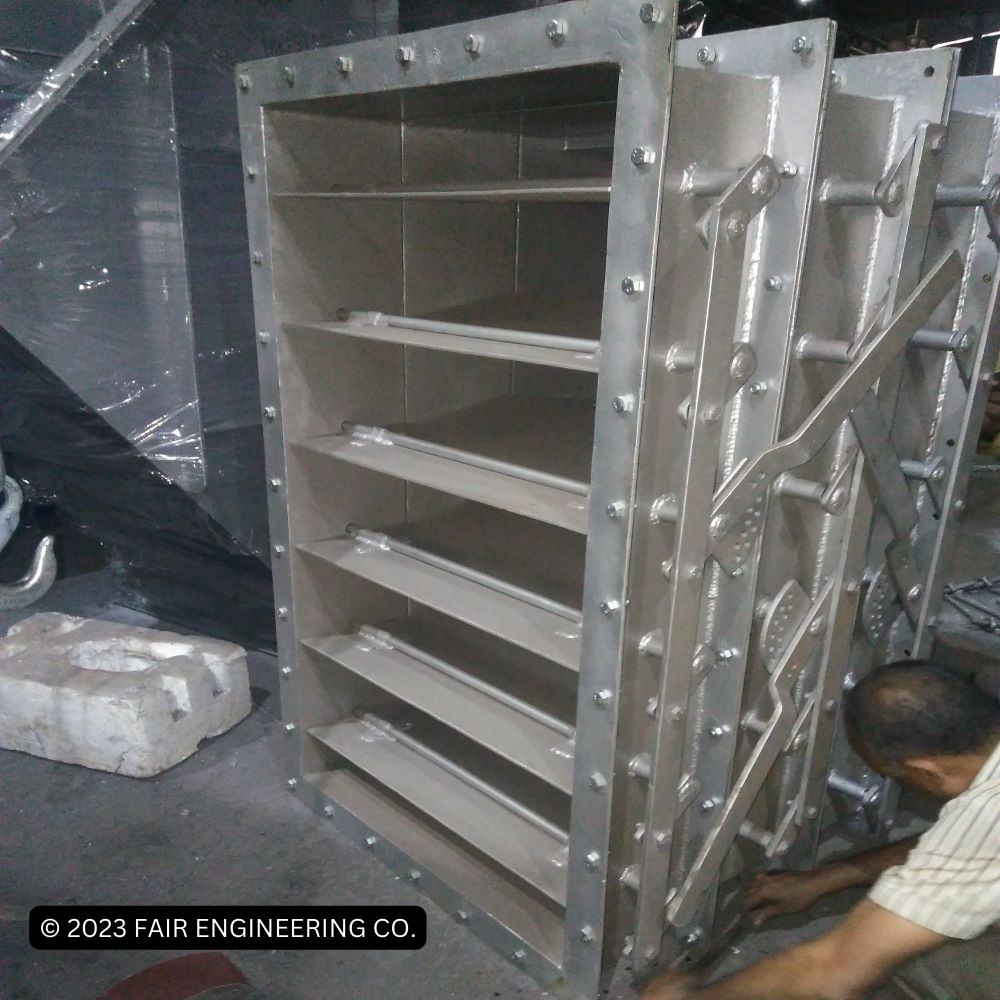
BUTTERFLY DAMPERS- MANUAL TYPE
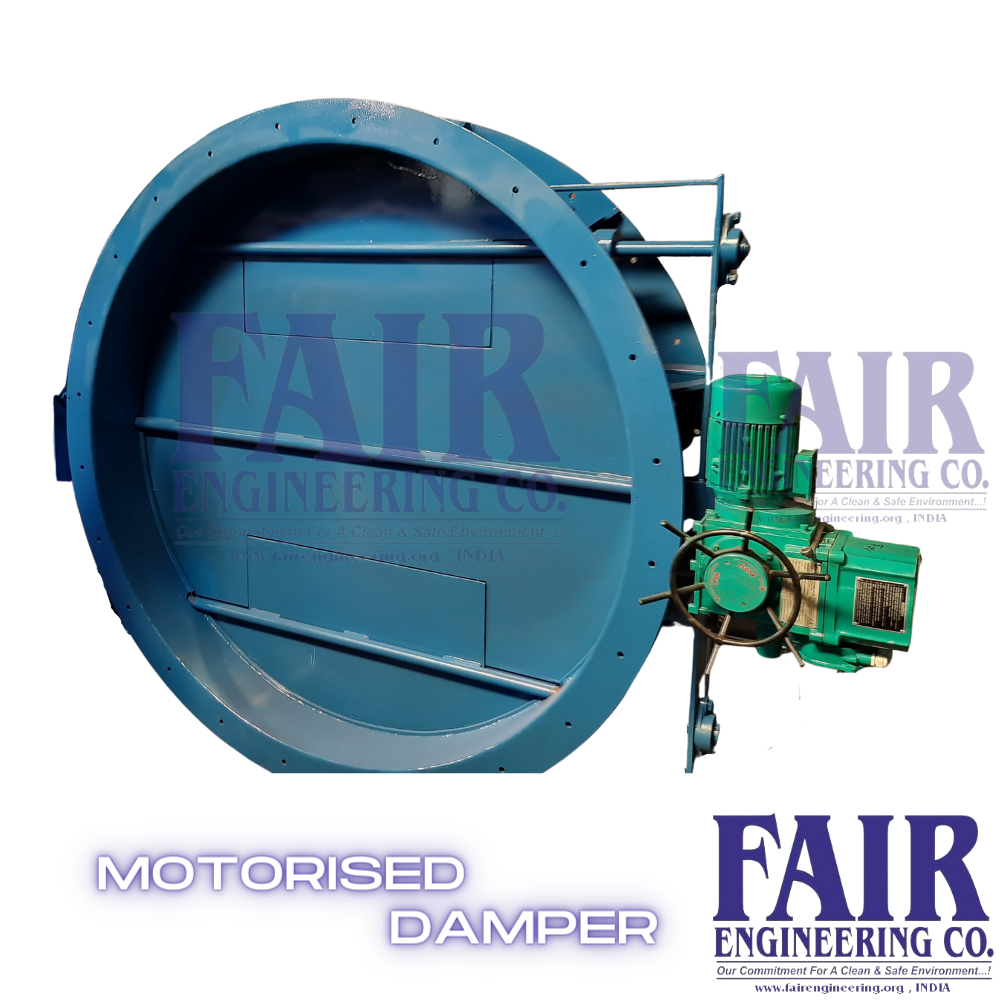
BUTTERFLY DAMPERS- MOTORISED TYPE
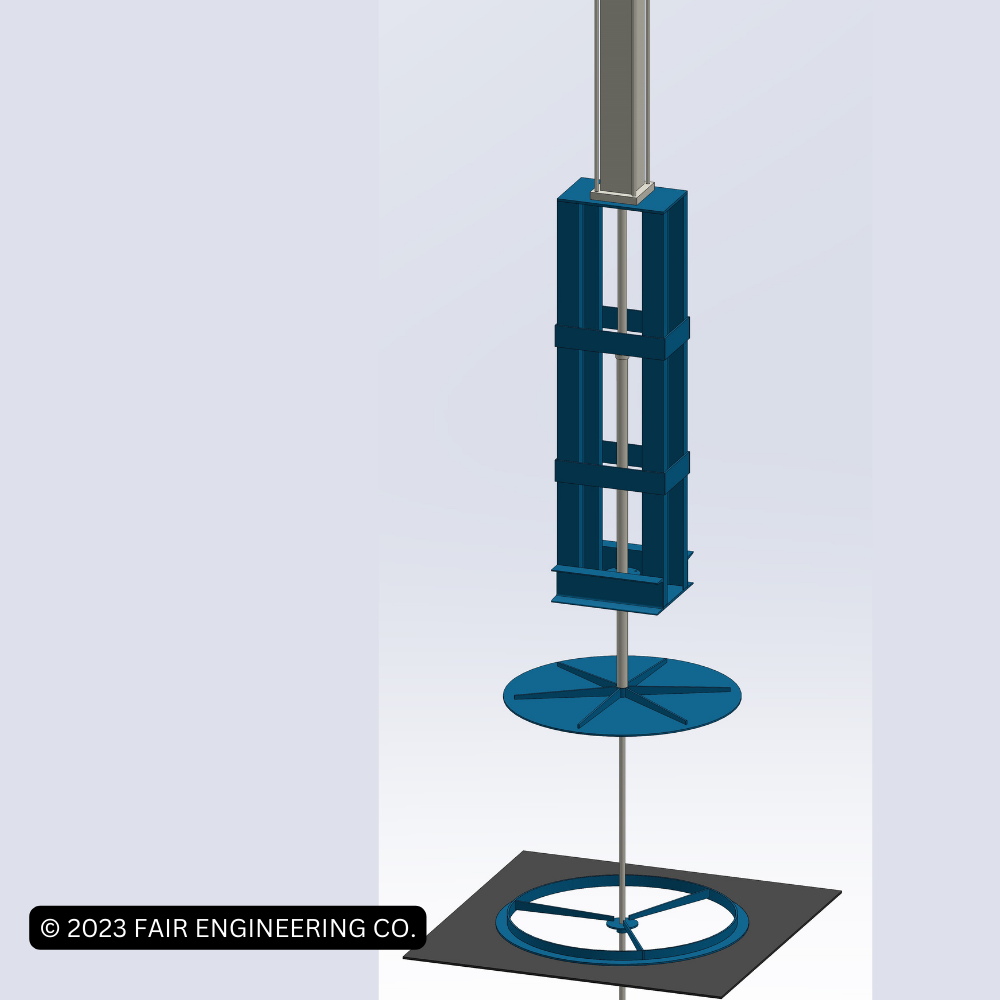
POPPET DAMPERS- PNEUMATIC TYPE
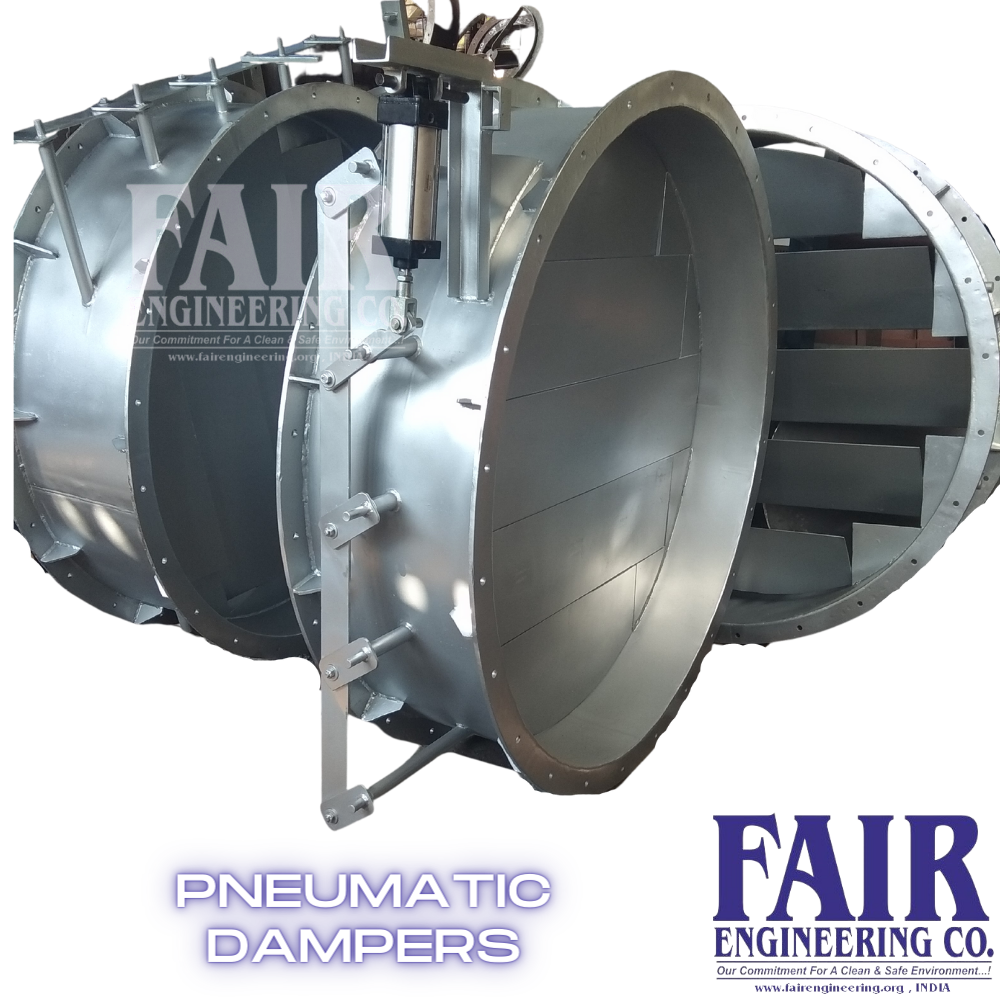
MULTI-LOUVER DAMPER- PNEUMATIC TYPE
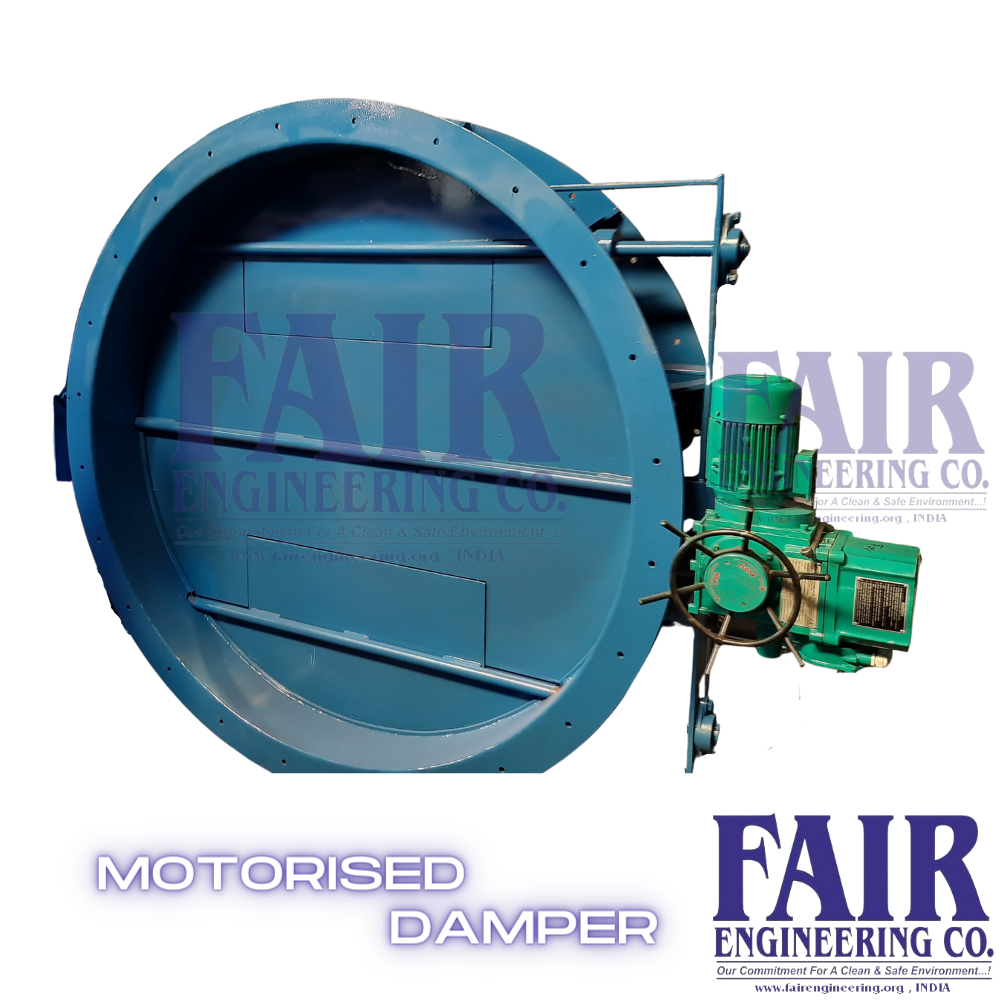
MULTI-LOUVER DAMPER- MOTORISED TYPE
INDUSTRIAL BLOWERS / AXIAL FANS
Fair Engineering consultants are SMEs in Air pollution system for steel plants. We have specialized knowledge of complete systems, equipment configuration and specifications. Our vendors and associates, manufacture blowers and ID fans based on our design calculations which are purely rated based on performance factors. Our blowers tend to provide a performance efficiency of more than 80% with maintenance free life of more than a year in continuous operation. We supply centrifugal and induced draft fans in range of 5000m3/hr to 500,000m3/hr and pressure ranges from 40mmWC to 1200mmWC for ambient air temperatures. Centrifugal fan with backward inclined blades that move air more efficiently than straight blade fans. BI fans are usually on the clean side of a piece of control equipment as the blades are not very abrasion resistant.
Types of Centrifugal Blowers and Induced Draft Fans
Centrifugal blowers and induced draft fans are two types of fans used to provide air flow in baghouse and dust collection systems. They are used to control air pollution in steel plants, in order to reduce emissions and ensure compliance with safety regulations. In this article, we will discuss the types of centrifugal blowers and induced draft fans, as well as their characteristics and applications in steel plant baghouse air pollution control systems.
Centrifugal blowers and induced draft fans are both mechanical devices that use a rotating impeller to generate air flow. Centrifugal blowers are used to create a pressure differential, moving air from areas of high pressure to areas of low pressure. Induced draft fans are used to draw air from an external source, such as a smokestack, and push it back through the system.
Centrifugal blowers are typically classified according to the type of impeller used. They can be divided into single-stage and multi-stage blowers, with single-stage blowers using a single impeller, and multi-stage blowers using multiple impellers. Induced draft fans are typically classified according to the type of blades used. They can be divided into backward-curved blades, radial blades, and forward-curved blades.
Characteristics of Centrifugal Blowers and Induced Draft Fans
Centrifugal blowers and induced draft fans each have unique characteristics that make them suited to specific applications. Centrifugal blowers are typically used when a high-pressure differential is required, such as in applications involving high temperatures or long duct runs. They are also often used in applications that require a low noise level, as they are typically more efficient and quieter than other types of blowers.
Induced draft fans are typically used when a low-pressure differential is required, such as in applications that involve large volumes of air. They are also often used in applications that require high air flow rates, as they can generate large volumes of air.
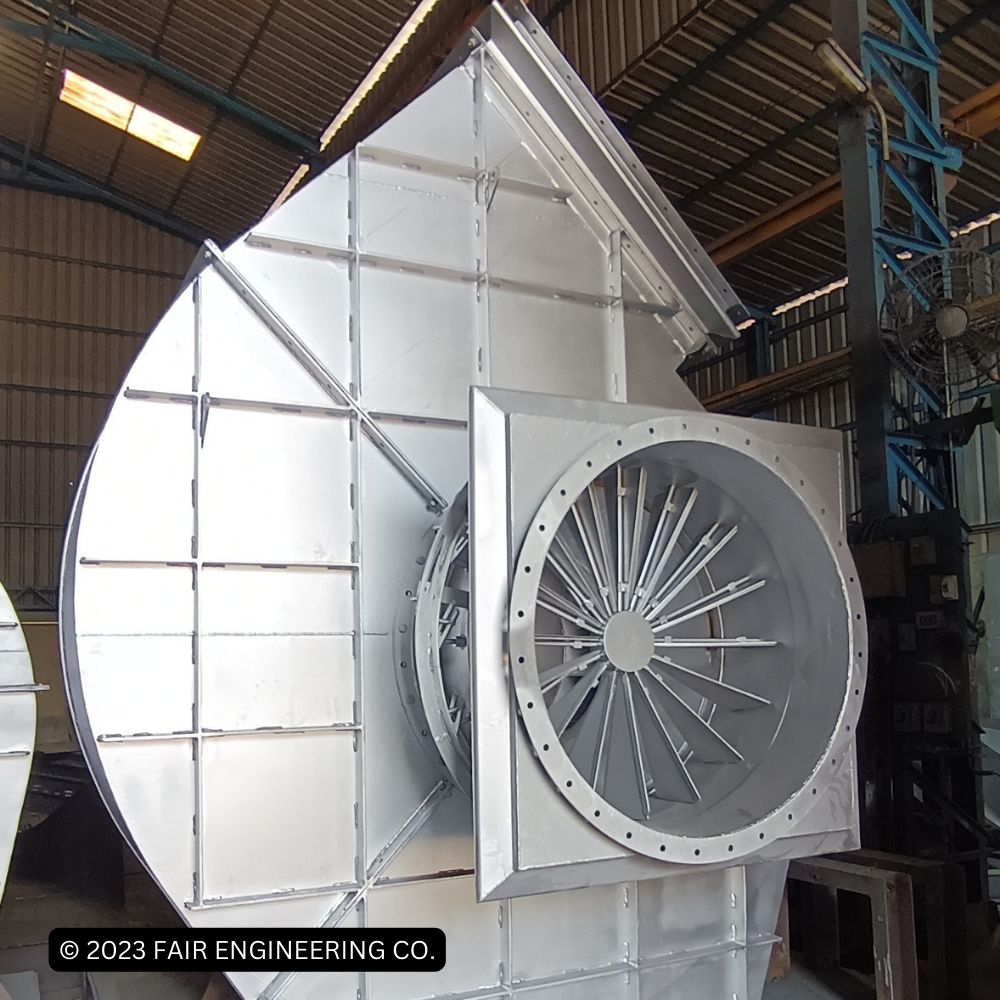
INDUSTRIAL BLOWERS
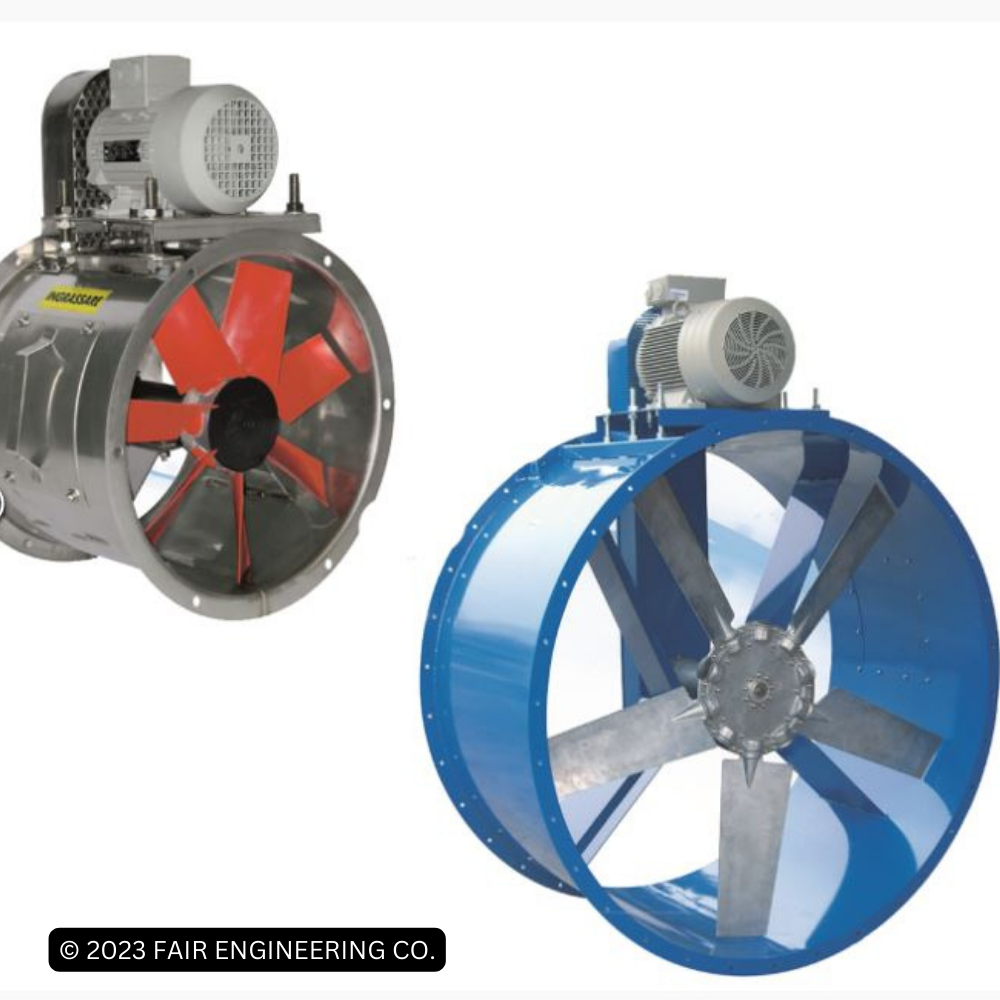
AXIAL FANS
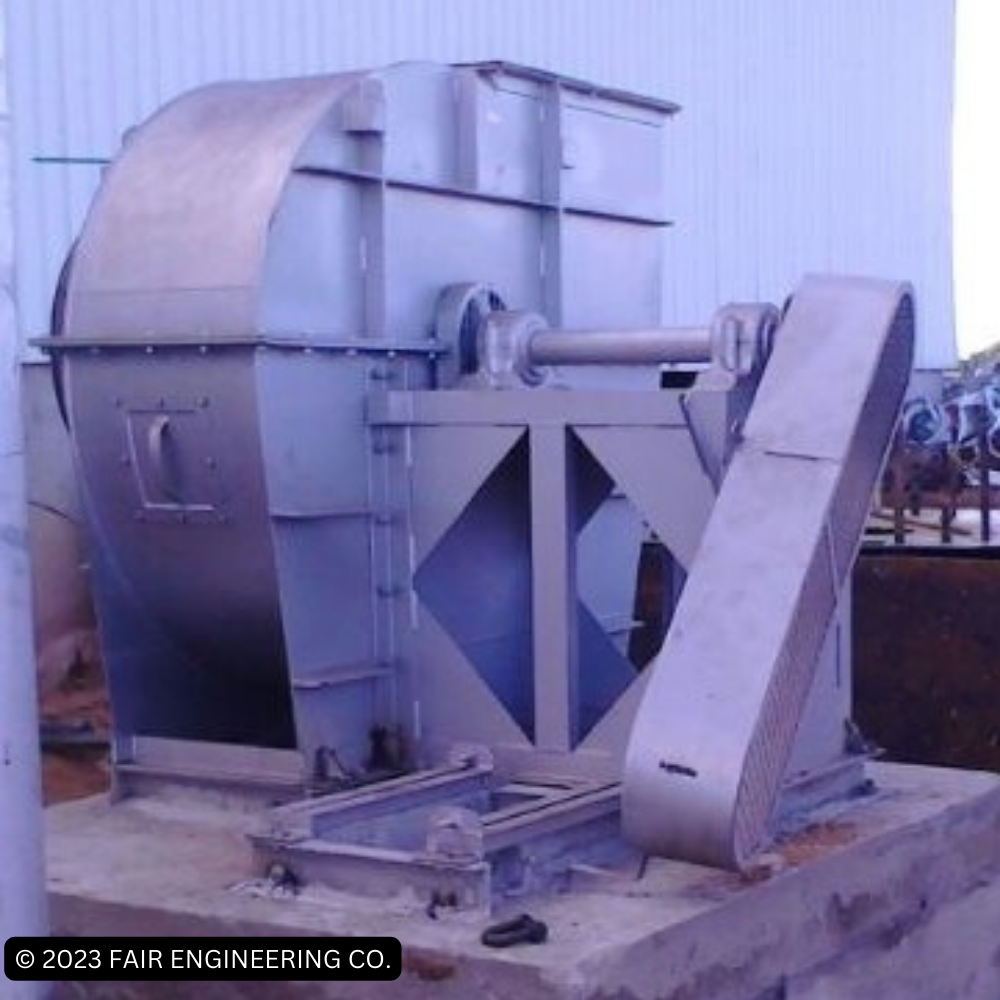
ID FANS
CHIMNEY / STACK
Industrial stacks or chimneys are tall structures used to expel filtered air from industrial sources. They are most commonly used in steel plants, power stations, and other factories where emissions such as smoke, dust, and other pollutants need to be expelled.
The size and height of stacks vary depending on the type of stack and the purpose for which it is used. For steel plants, the stacks are typically tall and narrow, with heights ranging up to 20 meters. The size of the stack depends on the amount of air expelled from the building and the nature of the emissions.
The fume suction for air pollution control system occurs from industrial blowers whereas the exhaust outlet of blowers is connected to stacks/ chimneys. These exhaust airs are filtered to around 10 to 100mg/Nm3 and discharged in atmosphere through the stacks.
The types of stacks used in steel plants include wet and dry stacks. Wet stacks are used for dispersing water vapor and other liquid emissions. They are often equipped with cooling systems and mist eliminators to minimize the emission of pollutants. Dry stacks, on the other hand, are used for expelling air, smoke, and dust. They may also be equipped with scrubber systems or bag house systems to filter the smoke out.
Overall, industrial stacks are an essential part of steel plants and other industrial facilities. In addition to expelling emissions, they also help reduce the noise produced while expelling air by the industrial blowers and make it more comfortable for workers to work in plants.
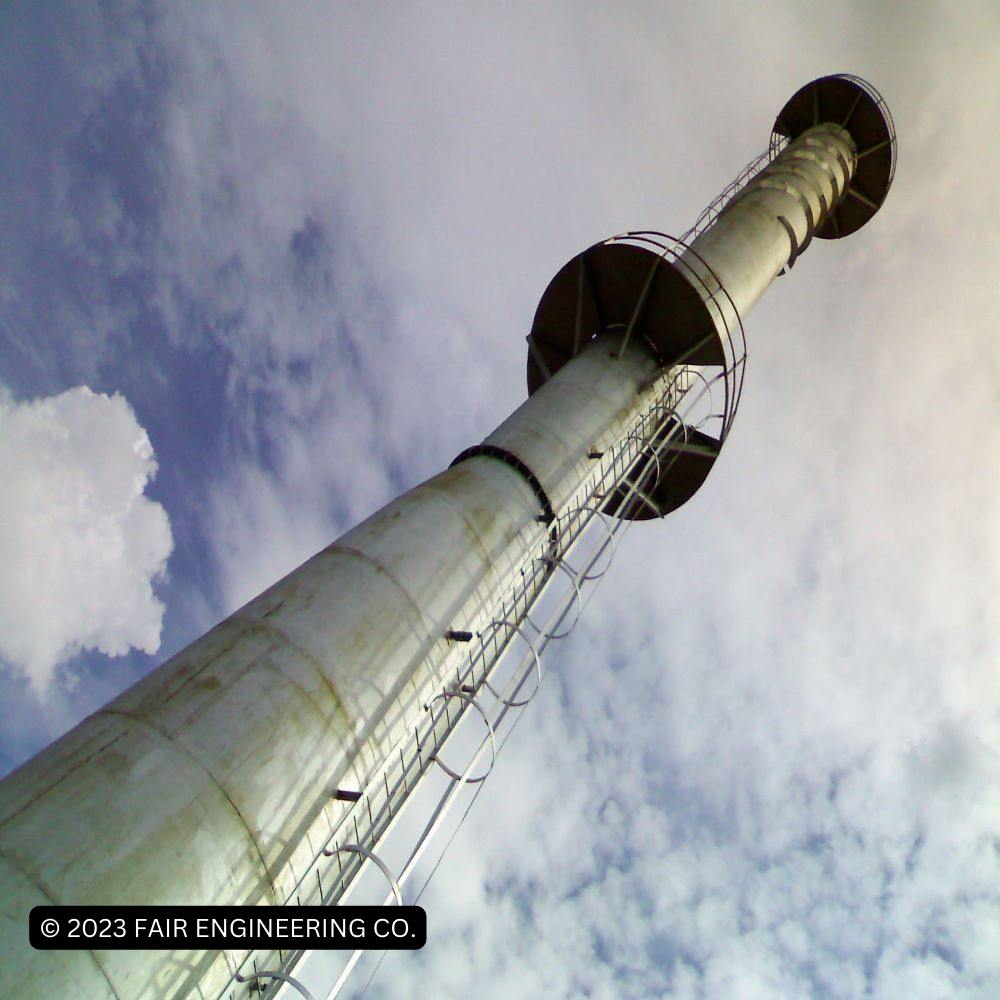
STACK

CHIMNEY
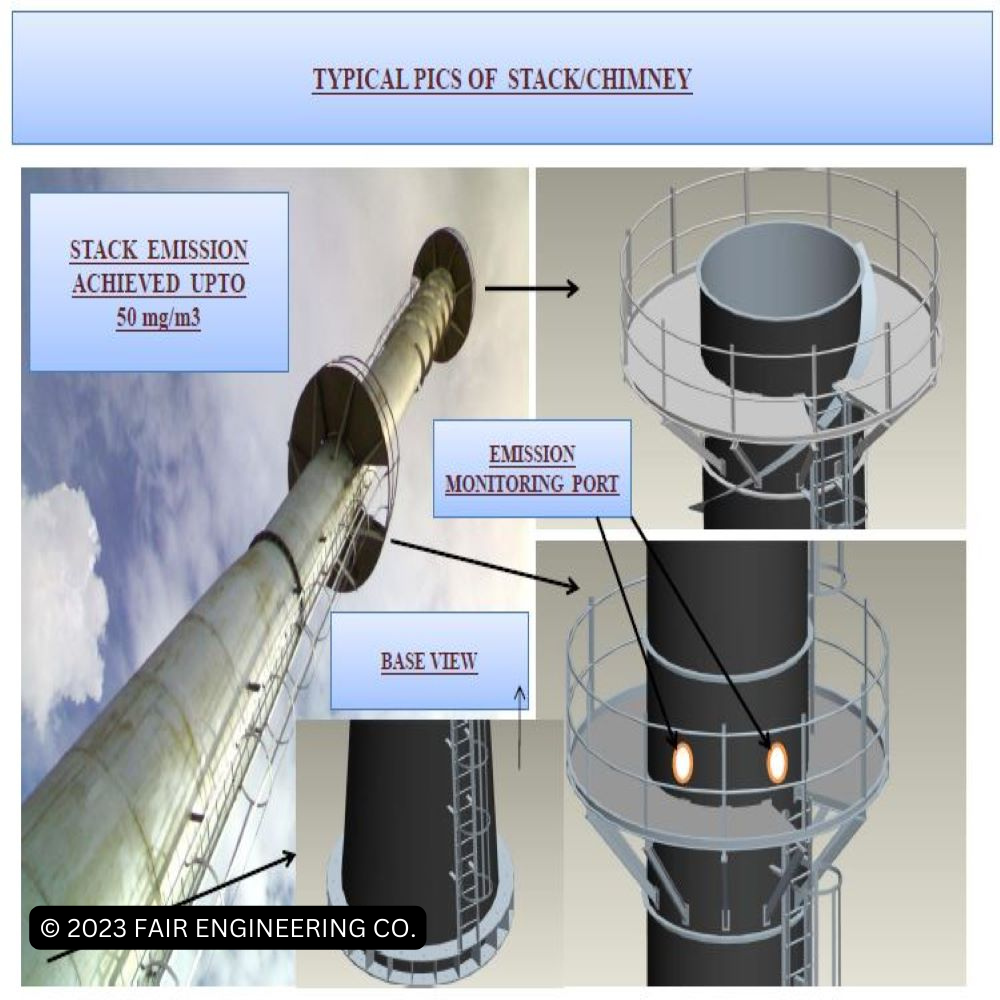
STACK DETAILS
ELECTRICAL COMPONENTS, TIMER CARD & VFDS
Fair Engineering Co. is pioneer is automation of FES system. All automation work is done inhouse by qualified engineers and commissioned at site by FEC team. We use the latest FEC designed timer card, MIMIC panels and branded configured VFD drives for all our electrical components such as geared motors, solenoid coils used for pulsing valves and pneumatic cylinders etc.
A solid-state sequential timer card is provided in IP-55 enclosure. The timer can be conveniently located near the bag filter. The input power supply is 220V/240V AC supply. The output from the timer is also 220V/240V AC that is fed to the solenoids which operate the pulse valves. The electrical terminations of the solenoid valves with that of the timer be done accordance with the drawing provided. The timers are housed in a sheet steel housing.
Understanding FEC Variable Frequency Drives for Electric Motors
Variable frequency drives (VFDs) are electronic controllers that can vary the speed of an electric motor by controlling the frequency and voltage of the power supplied to the motor. They enable precise control of motor speed and torque, which can provide several potential benefits to the user.
In this article, we will explore the benefits and drawbacks of using a VFD for electric motor control, and examine the components of a VFD system and how they are used to control the motor.
Benefits of Using a VFD
One of the biggest advantages of using a VFD to control an electric motor is that it can improve energy efficiency. By controlling the speed and torque of the motor, the VFD can reduce the amount of energy used during each cycle. This can reduce energy costs and save money in the long run.
Another advantage is that the VFD can provide dynamic control of the motor, allowing it to adjust its speed and torque as needed to meet changing conditions. This can provide greater flexibility and control over the motor’s operation.
Finally, VFDs can provide smoother starts and stops, reducing the amount of wear and tear on the motor and extending its useful life.
Components of a VFD System
A VFD system typically consists of three main components: the inverter, the motor, and the control panel. The inverter converts the incoming AC power into a DC signal, which the motor then uses to generate rotational force. The control panel is used to set the frequency and voltage of the power supplied to the motor, which in turn changes the speed of the motor.
Conclusion
VFDs can provide a number of benefits for electric motor control, including improved energy efficiency, dynamic control of the motor, and smoother starts and stops. However, they can also be expensive and require a more sophisticated level of maintenance than other solutions.

TIMER PANEL
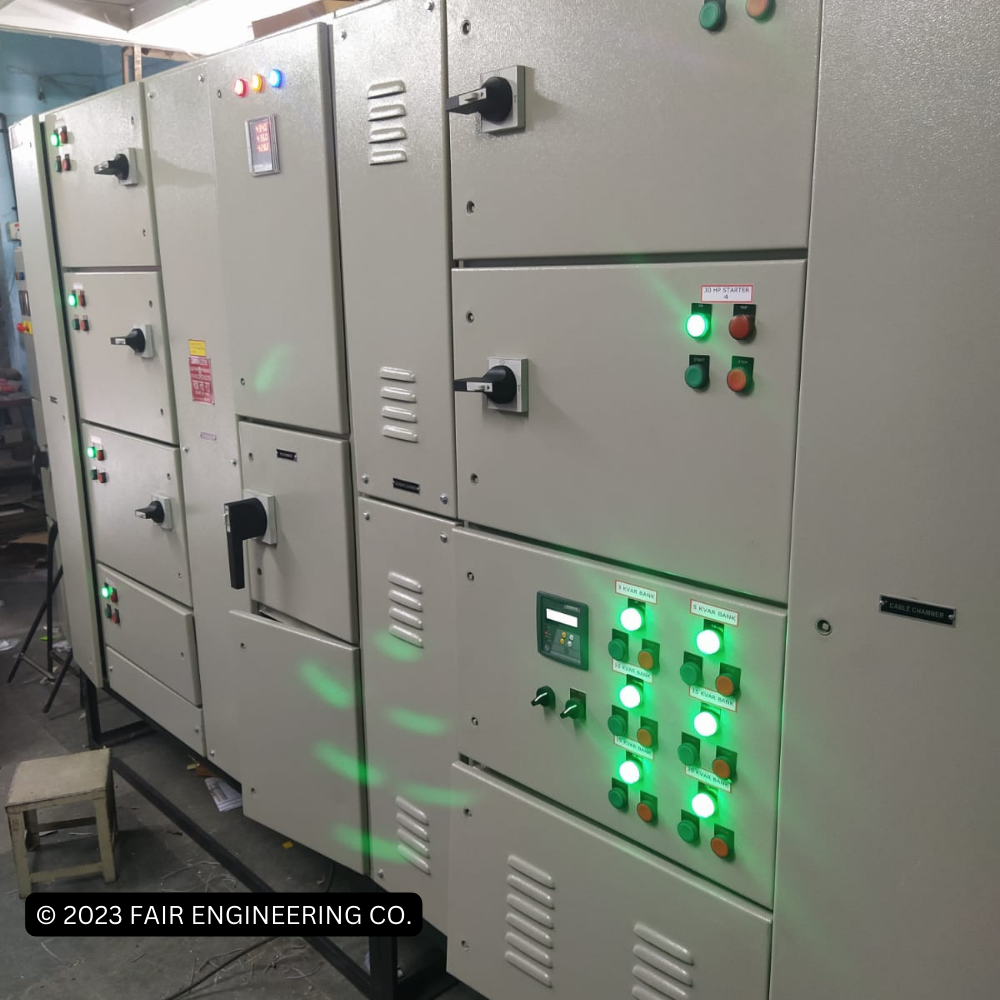
MCC CONTROL PANEL

GEARED MOTOR FOR RAV
INDUSTRIAL CYCLONE / DUST COLLECTOR
Industrial cyclones are a type of air pollutant control device used in steel plants to suck in and filter out fumes and contaminants from the air. They are typically used in the early stages of air pollution control, preceding the more advanced filtration systems. Cyclones rely on a centrifugal force to separate the particles, and can be highly efficient in capturing particulate matter of 50 µm or larger.
These are device used in many steel plants to separate and capture dust, particles, and other pollutants from the air in order to improve the air quality and protect employees and the environment. Industrial cyclones can be used to capture and control emissions from furnaces and other industrial processes, and are also used to reduce the amount of smoke, fumes, and dust released from steel plants.
The primary component of an industrial cyclone is a centrifugal force, or cyclone effect, which is created when air and particles are forced into a chamber and spun. This spinning motion causes the air and particles to separate, and the heavier particles are then directed downwards and collected in a container. The lighter particles are then directed upwards and out of the chamber, resulting in improved air quality.
Types of Cyclones
Industrial cyclones come in a variety of sizes and shapes, depending on the application. The most common type is the reverse-flow cyclone, which draws in contaminated air from the top and releases clean air from the side or bottom. This type of cyclone is commonly used in steel plants to capture large particles. The large particles are collected from hopper at the bottom.
Another type of cyclone is the parallel-flow cyclone, which takes in air from one end and releases it from the other. This type of cyclone is typically used for smaller particles, such as dust and smoke.
The Process
Cyclonic separation is a method of removing particulates from an air, gas or liquid stream, without the use of filters through. Rotational effect and gravity are used to separate mixtures of solids.
A high speeds rotating air flow is established within a cylindrical or conical container called a cyclone. Air flows in a helical pattern, beginning at the top (wide end) of the cyclone and ending at the bottom (narrow end) before exiting a cyclone in a straight stream through the centre of the cyclone and out the top. Larger (denser) particles in the rotating stream have too much inertia to follow the tight curve of the stream, and strike the outside wall, then falling to the bottom of the cyclone where they can be removed.
Advantages in Steel Plants
One of the main advantages of using an industrial cyclone in a steel plant is that it can reduce the amount of smoke, fumes, and dust released into the environment, thus decreasing the number of pollutants entering the atmosphere. This is particularly important in areas where air quality is already poor and is negatively impacting human health or the environment. Additionally, industrial cyclones can be used to help maintain higher air quality standards in steel plants, which can improve the working conditions for employees and reduce the risk of health and safety issues.
Another advantage of using industrial cyclones in steel plants is that they can reduce energy costs. These devices can help capture and trap particles and pollutants before they enter the exhaust system, which can reduce the amount of energy required to remove these particles from the air. This can help to lower energy costs in steel plants, which can lead to increased profits and improved efficiency.
In conclusion, industrial cyclones provide many advantages to steel plants, including improved air quality, lower energy costs, and improved safety and working conditions for workers. These devices can also help reduce the number of pollutants released into the environment, which can help protect human health and the environment. Industrial cyclones are a cost-effective and efficient way for steel plants to reduce their emissions and improve their overall efficiency.
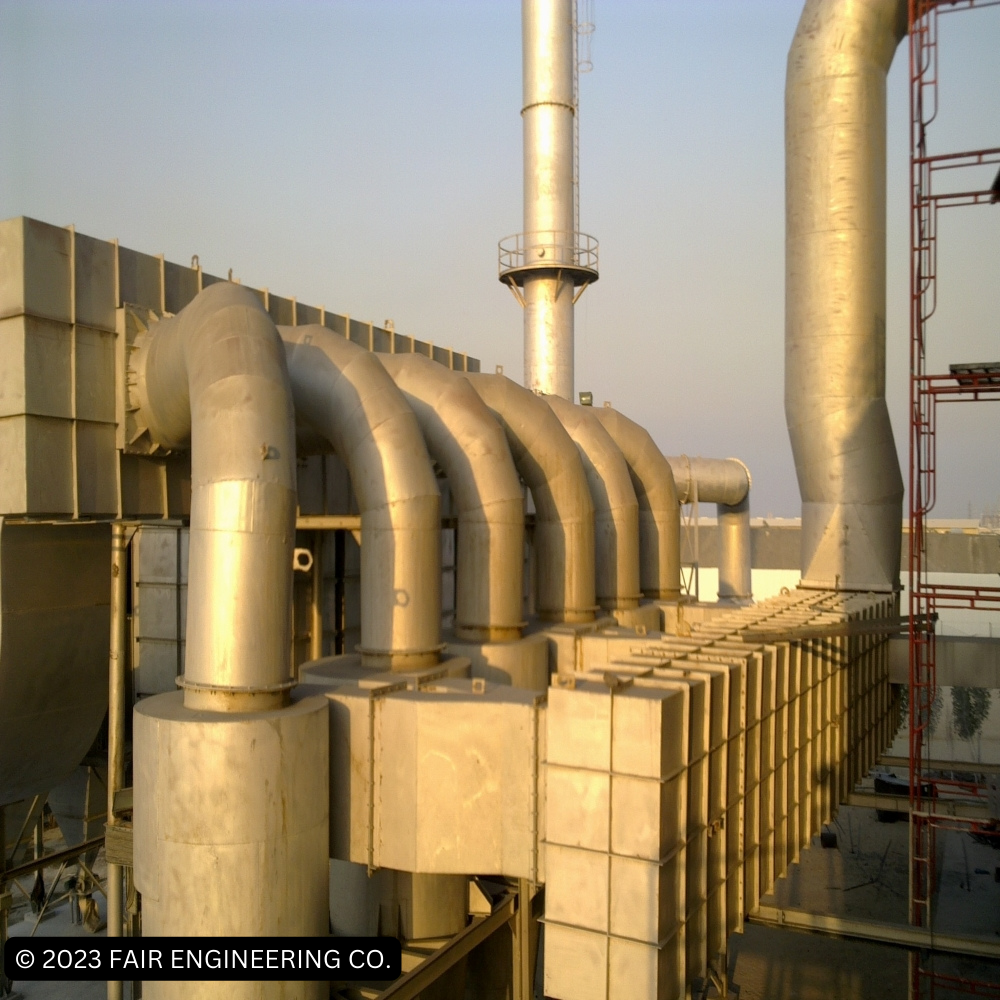
INDUSTRIAL MULTI-CYCLONE
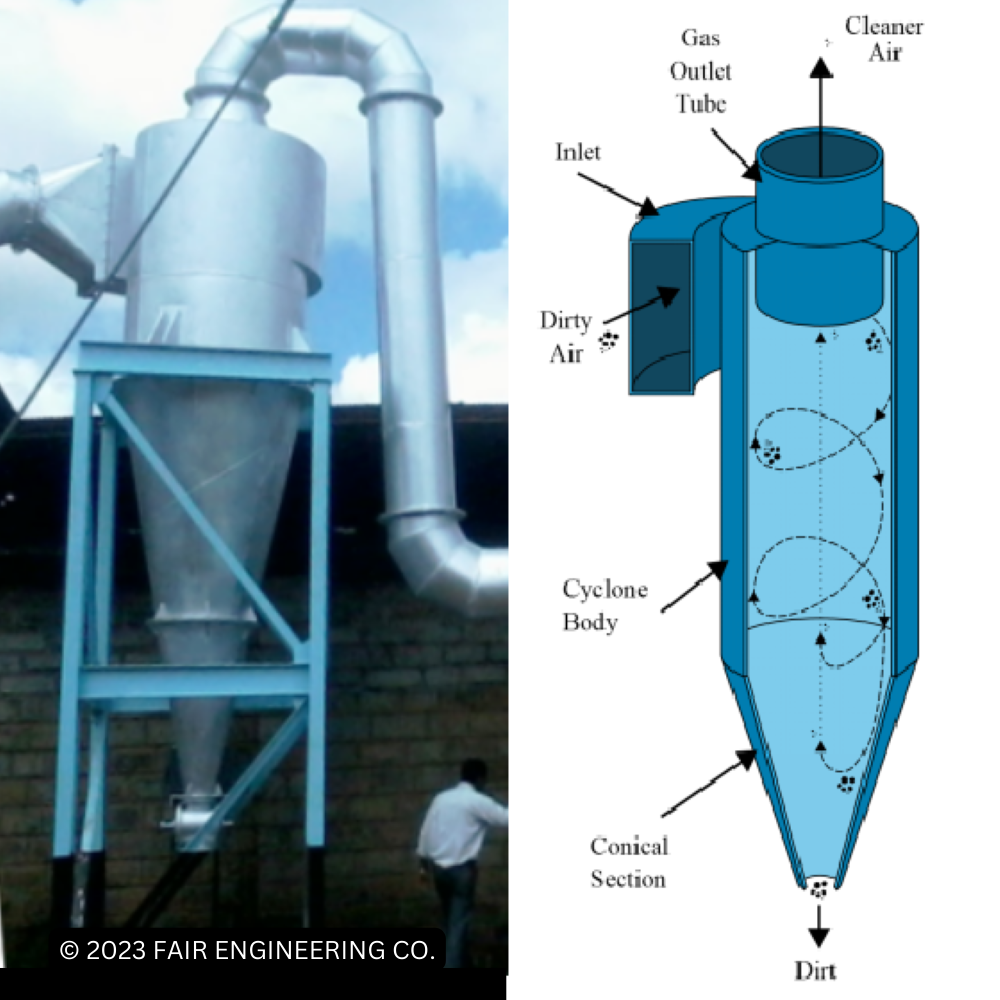
SINGLE CYCLONE
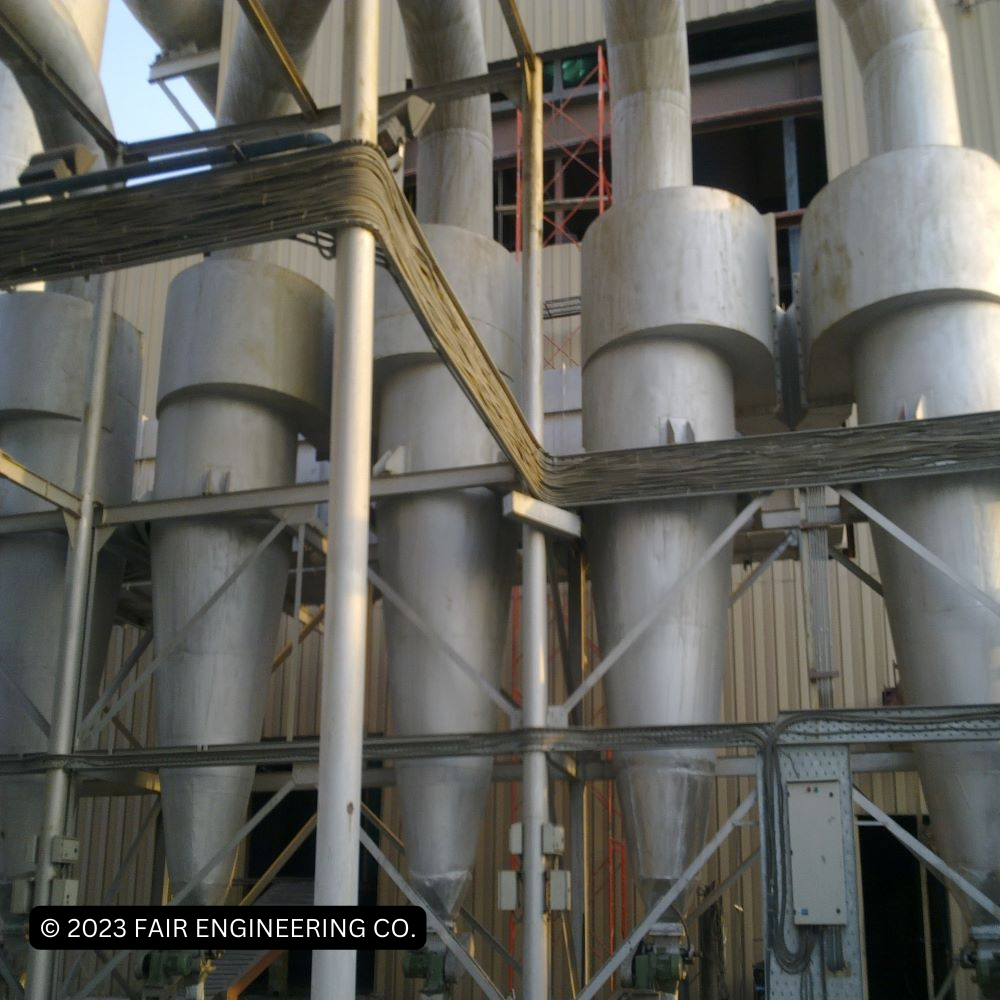
MULTI-CYCLONE
FORCED DRAFT COOLER
Forced draft coolers (FDCs) are air-cooled heat exchangers used to reduce the temperature of fume generated in steel plant pollution control systems. FDCs are used to cool down hot fumes with coarse particles produced by steelmaking processes, such as smelting, sintering, and other high-temperature operations in Induction, AOD or EAF type furnaces.
FDCs are often used in conjunction with other types of pollution control systems, such as baghouses and scrubbers. They can also be used in stand-alone applications to reduce the temperature of fumes and other noxious gases.
The primary benefit of using an FDC is that it can reduce the temperature of hot, polluted air by as much as 50-60 °C. Also, the coarse particles in fumes gets settled in the hopper and only fine dust is allowed to exhaust in the bag filter system. This can help the other pollution control equipment’s after FDC to operate more effectively by lowering the temperature of the air they need to filter. It can also reduce the energy costs associated with cooling the hot fumes.
FDCs are easy to install and maintain, and require only minimal space to operate. They are also more efficient compared to other cooling methods such as wet scrubbing, and can reduce the overall energy costs of a steel plant’s pollution control system.
Overall, using an FDC can be a cost-effective way to reduce the temperature of hot, polluted air in steel plant pollution control systems. It can help to improve the efficiency of other pollution control systems, and can reduce energy costs associated with cooling the air.
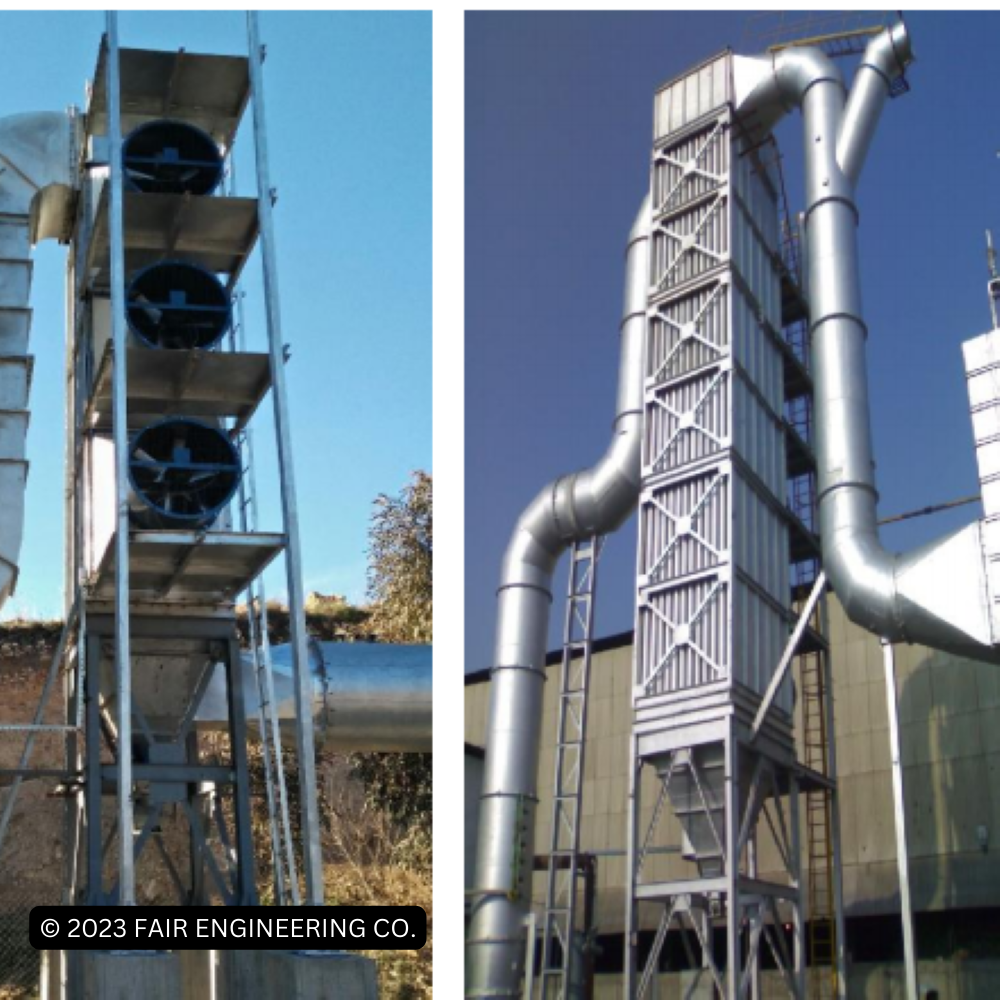
FORCED DRAFT COOLER

FORCED DRAFT COOLER

FORCED DRAFT COOLER
WATER COOLED BENDS AND DUCTINGS
In the realm of industrial pollution control, effective extraction and management of hot fumes and dust is of paramount importance. Steel plants, in particular, face the challenge of efficiently handling these emissions to ensure a safe and sustainable working environment. One crucial component that aids in this endeavor is water-cooled ducting and bends made from 50nb ERW MS pipes.
Advantages of Water-Cooled Ducting and Bends
- Heat Dissipation: Water-cooled ducting and bends excel at dissipating heat generated by hot fumes in steel plants. By utilizing a flow of water, they effectively absorb and carry away thermal energy, preventing excessive temperatures that could compromise the integrity of the ducting and endanger personnel.
- Enhanced Durability: The usage of 50nb ERW MS pipes, known for their strength and corrosion resistance, ensures the longevity and reliability of the ducting system. The robust nature of these pipes allows them to withstand high temperatures, harsh environments, and corrosive substances commonly found in steel plants.
- Improved Efficiency: The cooling effect provided by water-cooled ducting optimizes the efficiency of the pollution control system. By reducing the temperature of the fumes and dust, the system can more effectively capture and extract pollutants, preventing their release into the atmosphere.
- Energy Conservation: Water-cooled systems are energy-efficient alternatives to traditional air-cooled counterparts. By utilizing water as a cooling medium, these systems can minimize the energy consumption associated with cooling mechanisms, leading to cost savings and reduced environmental impact.
Uses of Water-Cooled Ducting and Bends in Steel Plants
- Suction of Hot Fumes: The primary application of water-cooled ducting and bends is the suction of hot fumes produced in various processes within steel plants. Whether it is the smelting of iron ore, steelmaking, or other high-temperature operations, these ducting systems efficiently extract and transport the fumes to the pollution control devices.
- Dust Extraction: In addition to fumes, steel plants generate substantial amounts of dust and particulate matter. Water-cooled ducting and bends play a vital role in the extraction of these pollutants, ensuring a cleaner and healthier work environment.
Technical Aspects of Water-Cooled Ducting and Bends
- Material: Water-cooled ducting and bends are constructed using 50nb ERW MS pipes. These pipes are made from electric resistance-welded mild steel, which possesses excellent mechanical properties, including high tensile strength and resistance to corrosion and thermal stress.
- Water Circulation: A closed-loop water circulation system is employed to cool the ducting and bends. Water is pumped through the system, absorbing heat from the ducting and dissipating it through a heat exchanger or cooling tower. The cooled water is then recirculated, ensuring a continuous cooling process.
- Structural Design: Water-cooled ducting and bends are designed to withstand high temperatures and maintain structural integrity. The ducting is insulated to minimize heat loss and prevent the external surface temperature from rising to hazardous levels. Additionally, the bends are carefully engineered to maintain efficient airflow and minimize pressure drop.
Conclusion
Water-cooled ducting and bends made from 50nb ERW MS pipes represent an advanced solution for the extraction of hot fumes and dust in steel plants. With their heat dissipation capabilities, enhanced durability, improved efficiency, and energy conservation benefits, these systems contribute significantly to the engineering, procurement, and construction of pollution control systems. By implementing these innovative solutions

WATER COOLED DUCTING
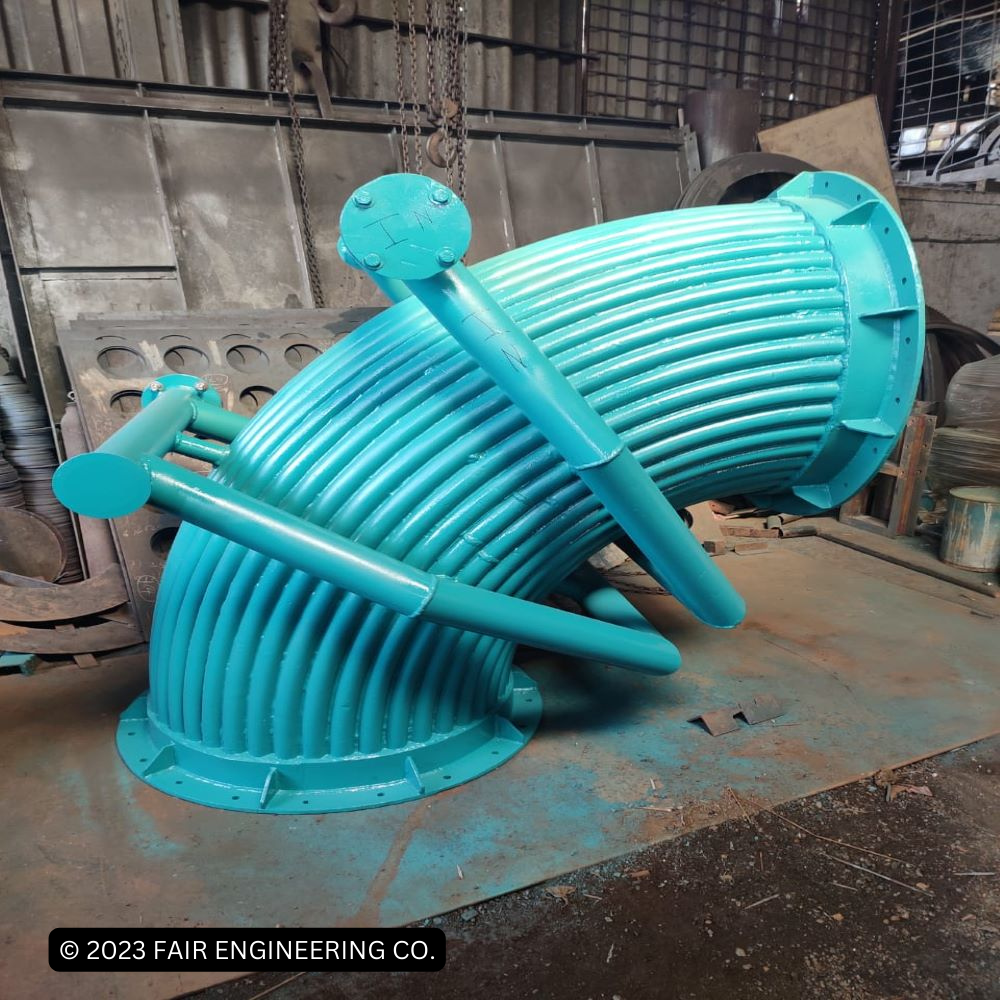
WATER COOLED 90 DEG BEND
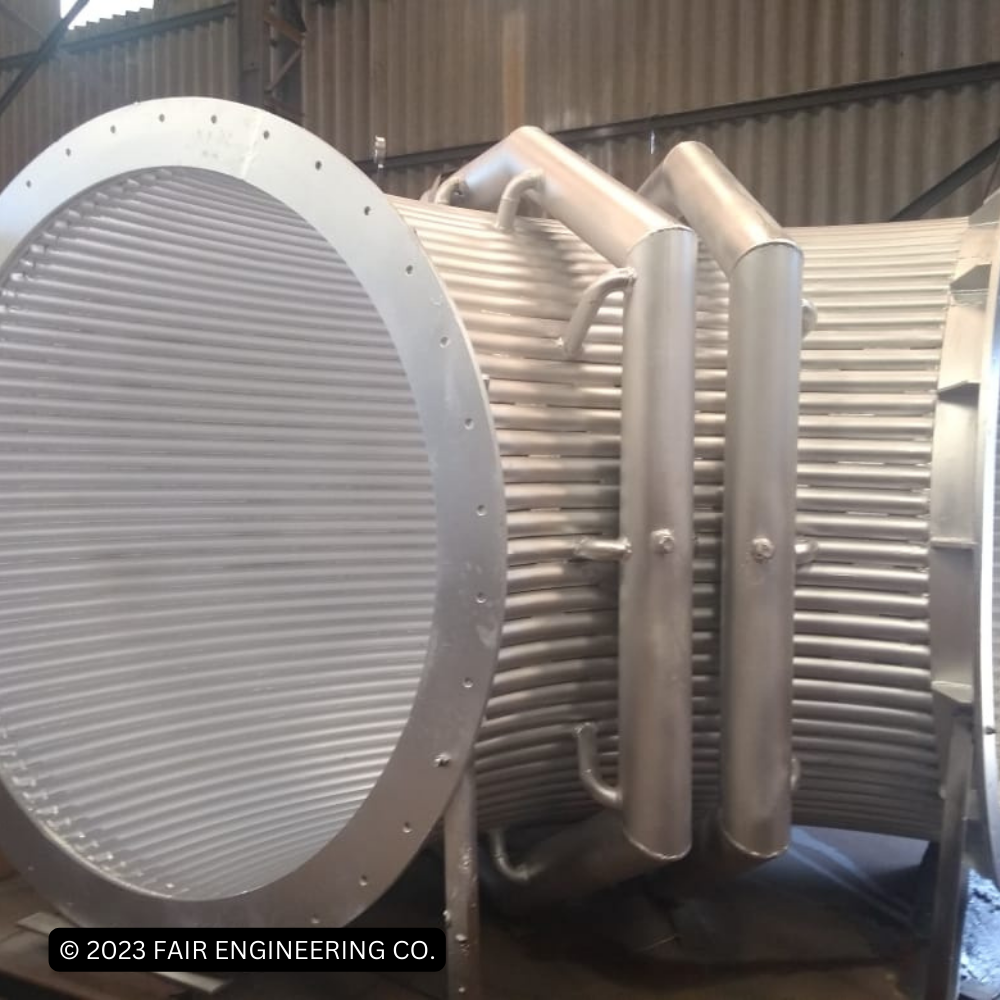
WATER COOLED BEND WITH HEADERS
MATERIAL HANDLING EQUIPMENTS- VIBRO FEEDER
Vibro-feeders are an essential part of modern material handling systems in industrial plants. They are used to convey or feed materials at a consistent rate, helping improve the efficiency of production and reduce labour costs.
What Is a Vibro-Feeder?
A vibro-feeder is a device that uses vibration to dispense material in constant flow. It is often used in industrial processes to help control the speed and volume of material being dispensed. The vibration of the device helps to ensure a consistent feed rate, and it can be adjusted to control the speed of the material.
Benefits of Using Vibro-Feeders
Vibro-feeders offer several benefits to industrial processes. They can help reduce labour costs by eliminating the need for manual labour to move materials. They can also help to reduce the need for additional equipment such as hoists or other lifting devices. Additionally, they can help reduce the need for costly maintenance and repairs as the vibration of the vibro-feeder helps to reduce damage to the material being managed
How Are Vibro-Feeders Used?
Vibro-feeders are used in a variety of industrial processes, from material handling to processing. They can be used to move large amounts of material quickly and efficiently, helping to reduce overall labor costs and production time. For example, they are often used in assembly lines to move parts from one station to another in a continuous and consistent manner. They can also be used in manufacturing processes to help move material through a process or to ensure a consistent feed rate for industrial furnace.
Safety Considerations
Vibro-feeders are powerful pieces of equipment and should be treated with care. They should be regularly inspected and maintained to ensure they are functioning properly and safely. Additionally, staff should be properly trained and instructed on how to operate the device and how to troubleshoot any issues that may arise.
Overall, vibro-feeders can be a great addition to any industrial material handling system. They offer efficient and cost-effective material movement, helping to reduce labour costs and improve production times. They are also relatively easy to operate and maintain, making them a great choice for industrial processes.

VIBRO FEEDER
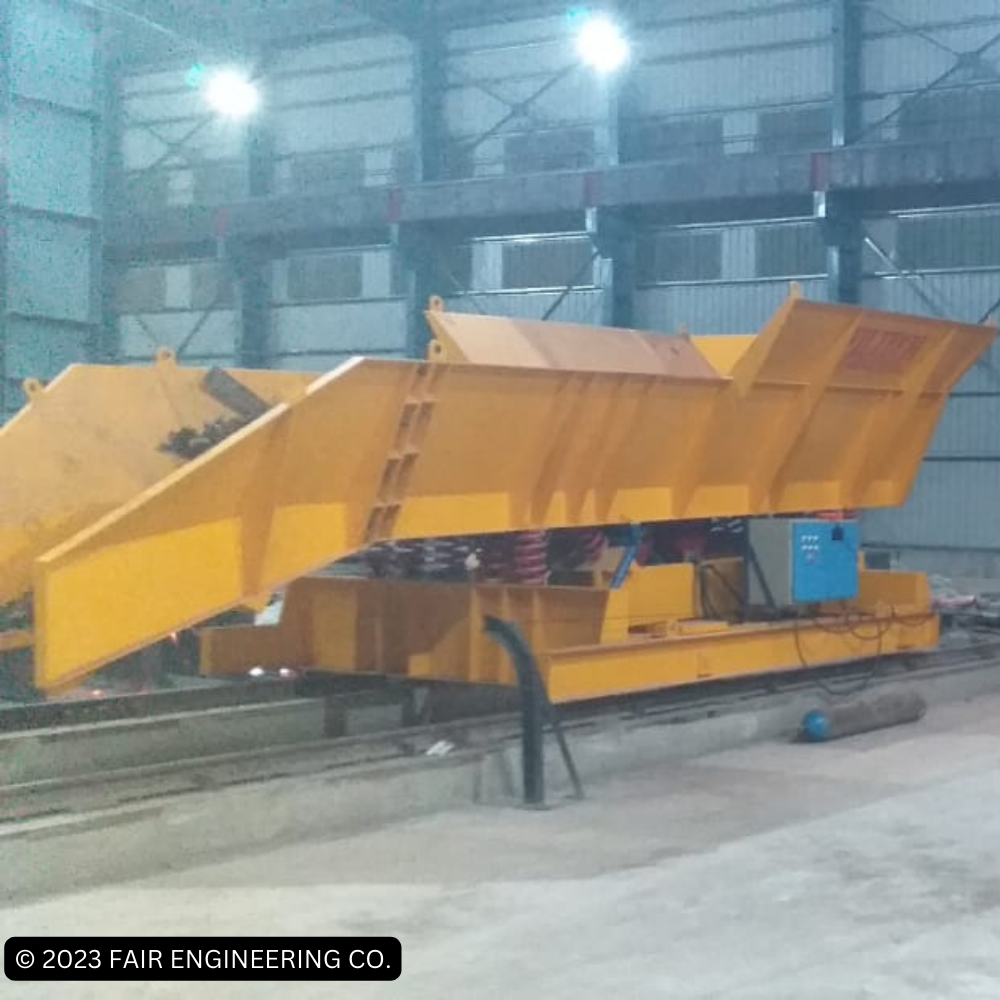
VIBRO FEEDER
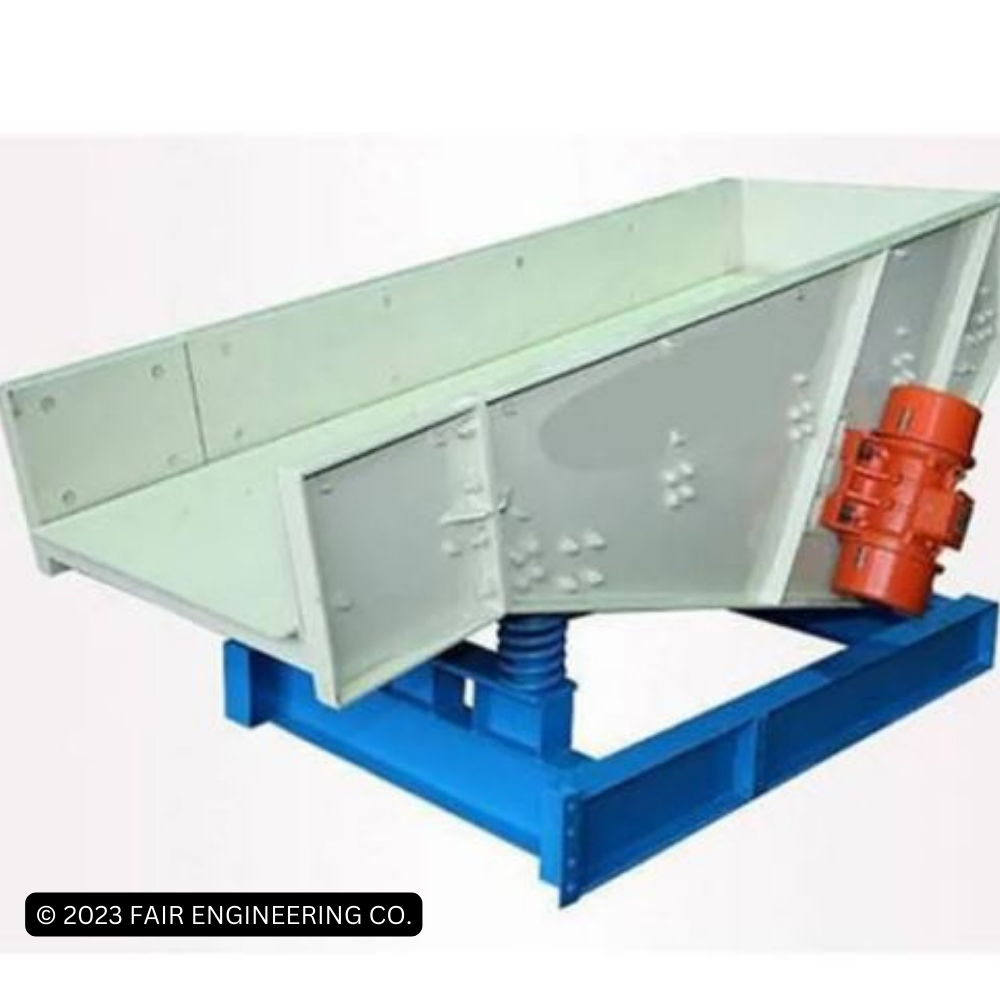
VIBRO FEEDER
MATERIAL HANDLING EQUIPMENTS- CONVEYORS
At Fair Engineering Company, we specialize in providing comprehensive engineering, procurement, and construction services for pollution control systems in various industries. One of our key areas of expertise lies in the design, manufacture, and installation of advanced conveyor systems for steel plants, mining operations, and cement plants. In this article, we will focus on three commonly used conveyor types: Screw Conveyors, Belt Conveyors, and Scraper Conveyors. These versatile systems play a vital role in enhancing productivity, efficiency, and safety within these industries.
- Screw Conveyors: Screw conveyors are an integral part of material handling systems in steel plants, mining, and cement plants. They are used for conveying bulk materials such as ores, coal, aggregates, and cement powders. The key features of screw conveyors include:
- Flexible design options to suit specific requirements, including various screw configurations and flight types.
- Efficient transportation of materials over short to medium distances.
- Ability to handle various material types, sizes, and consistencies.
- Easy maintenance and accessibility for cleaning or maintenance tasks.
- Options for special coatings or materials to withstand corrosive or abrasive environments.
- Belt Conveyors: Belt conveyors are widely utilized in steel plants, mining operations, and cement plants due to their high capacity and reliability. These conveyors consist of a continuous belt that moves over pulleys, allowing for the smooth transportation of materials. The key features of belt conveyors include:
- High capacity and long-distance conveying capabilities.
- Versatile design options to accommodate various material types, sizes, and weights.
- Ability to handle both bulk materials and unit loads efficiently.
- Excellent reliability with low maintenance requirements.
- Optional features such as covers, dust suppression systems, and belt cleaners for improved safety and environmental control.
- Scraper Conveyors: Scraper conveyors, also known as drag chain conveyors, are commonly used in steel plants, mining operations, and cement plants for handling materials such as sludges, wet ash, and sticky substances. These conveyors employ a chain with attached scrapers to move materials along a trough. The key features of scraper conveyors include:
- Effective handling of wet, sticky, or abrasive materials.
- Robust construction to withstand harsh operating conditions.
- Ability to handle both horizontal and inclined conveying.
- Low power consumption and energy-efficient operation.
- Various scraper designs available for specific material characteristics and application requirements.
Fair Engineering Company takes pride in offering advanced conveyor systems tailored to the specific needs of steel plants, mining operations, and cement plants. Screw conveyors, belt conveyors, and scraper conveyors are just a few examples of the wide range of conveyor solutions we provide. Our expertise in engineering, procurement, and construction ensures that our clients receive high-quality, efficient, and reliable systems that contribute to improved productivity, streamlined operations, and enhanced environmental control. Contact us today to learn more about our comprehensive range of conveyor systems and how we can assist in implementing pollution control solutions for your industry.

SCREW CONVEYOR

BELT CONVEYOR

SCRAPER CONVEYOR
TROLLEY FOR WATER COOLED HOOD OF AOD
TO BE UPDATED
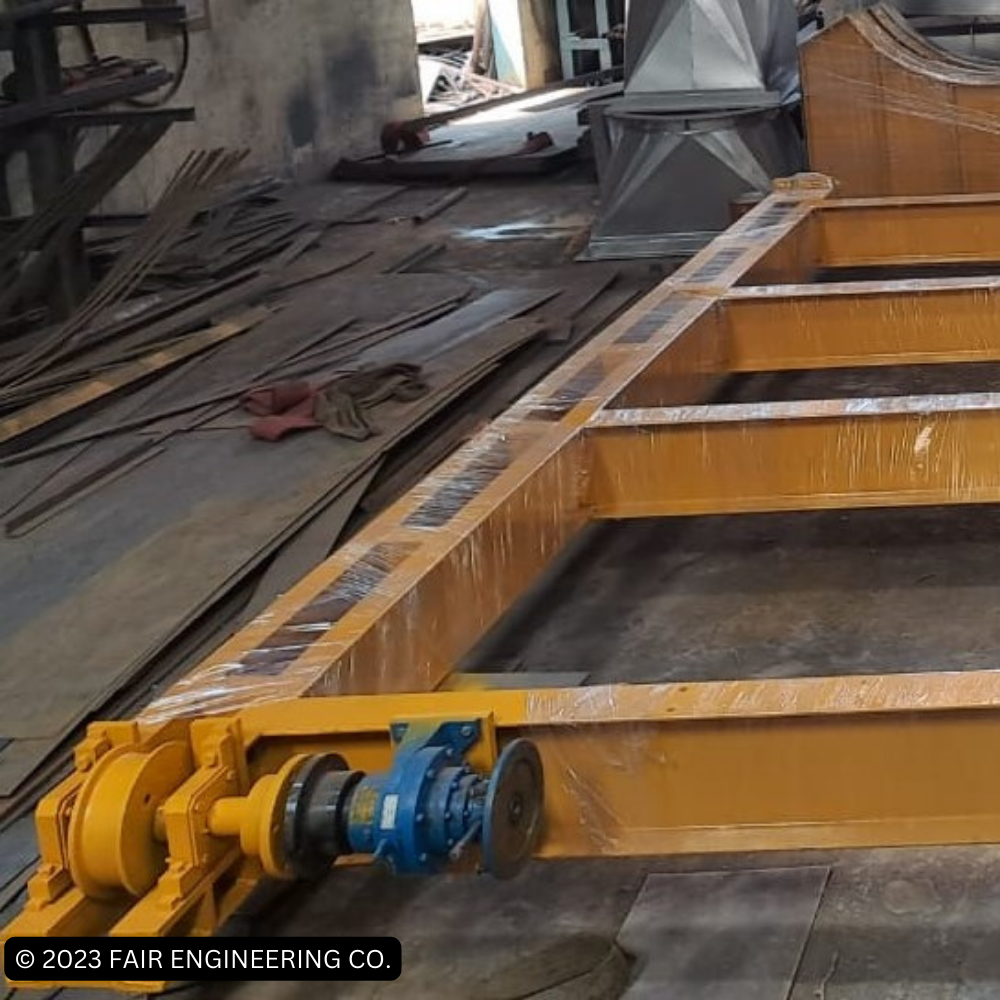
TROLLEY MFG FOR AOD HOOD
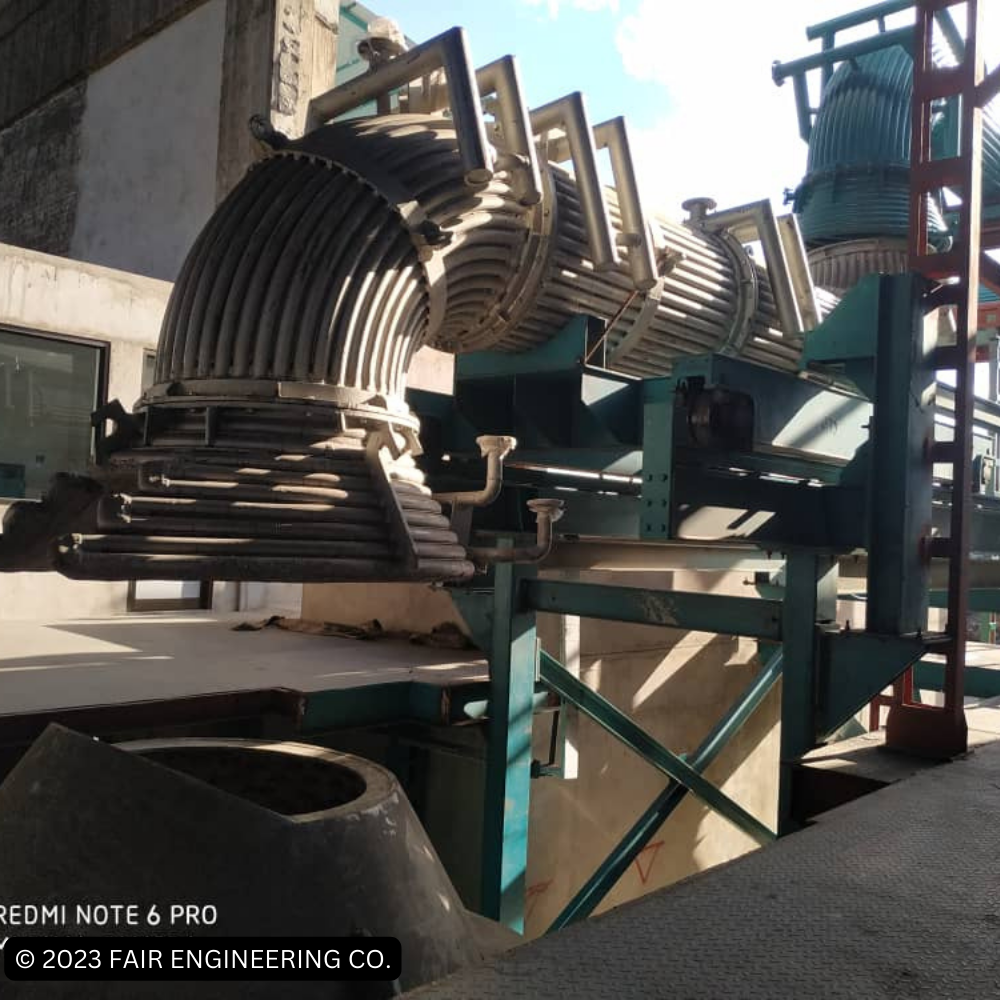
TROLLEY INSTALLATION FOR AOD
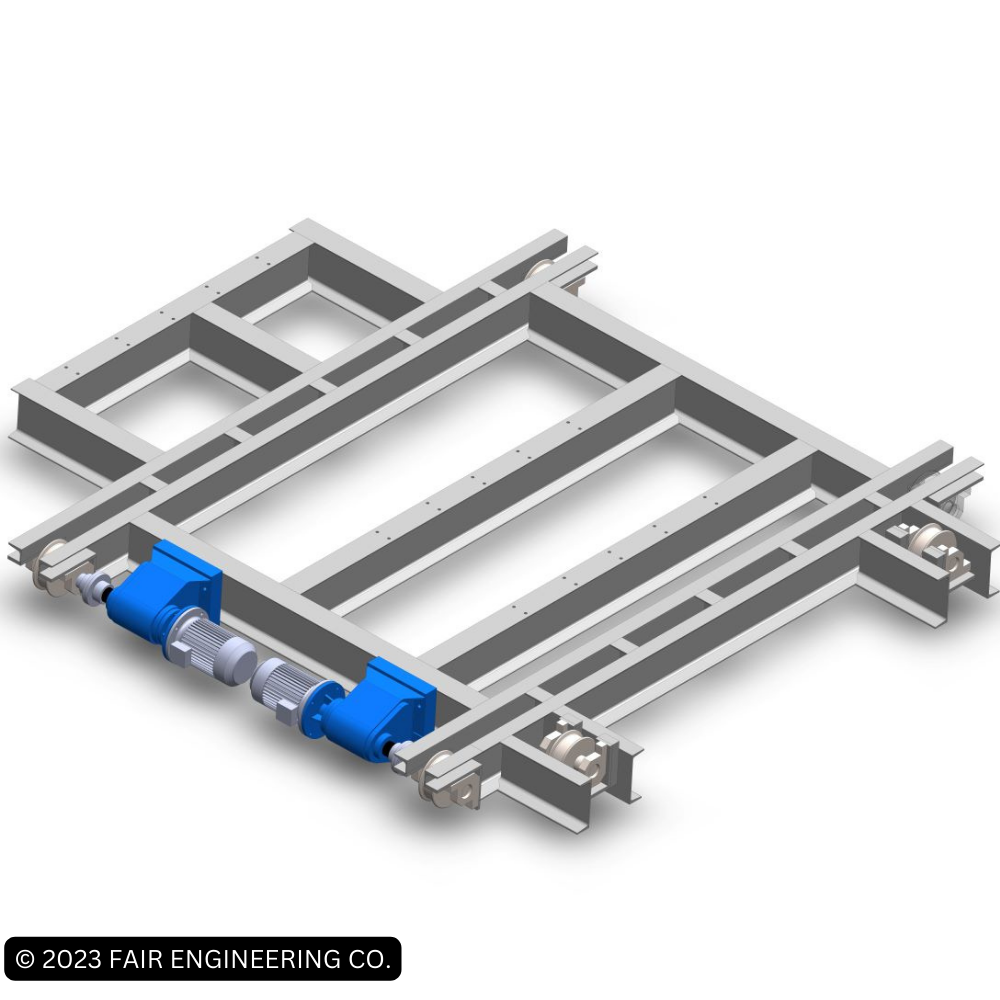
TROLLEY FOR AOD HOOD -3D
SWIVEL BEARING FOR HOODS
FEC swivel bearing is a special product which provides flexibility of rotational moment to canopy hoods or side draft hoods. We design and manufacture swivel bearings in-house. The product involves a round duct which are interconnected having ball bearings set encapsulated inside the bearing housing fabricated around the ducting area. The bearing moment is controlled by a worm gear which is connected to geared motor fabricated on the side of ducting stand. There is end to end flange connections so the product can be assembled in between the raised ducting above the furnace platform. A side draft or canopy hood is then installed above the bearing flange connections. The bearing facilitates swivel moment of 180° to facilitate fume suction from alternate induction furnaces.
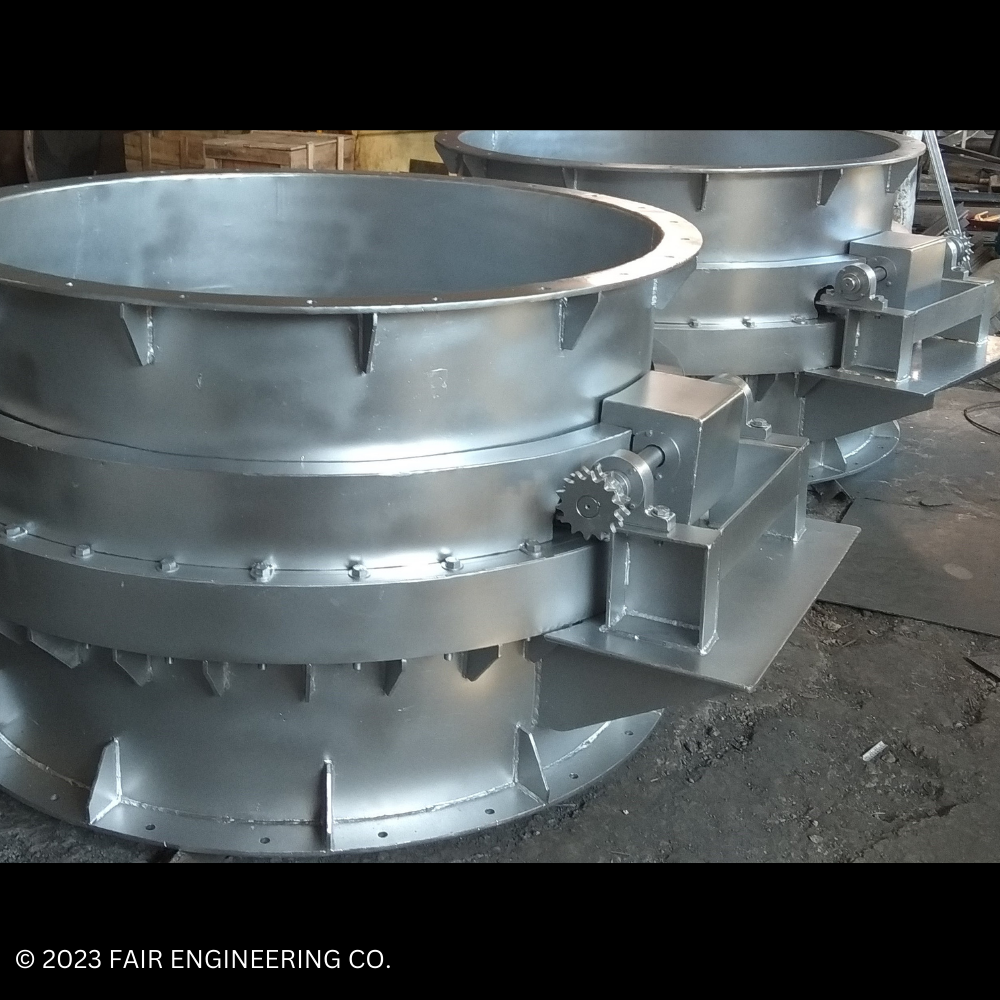
SWIVEL BEARING
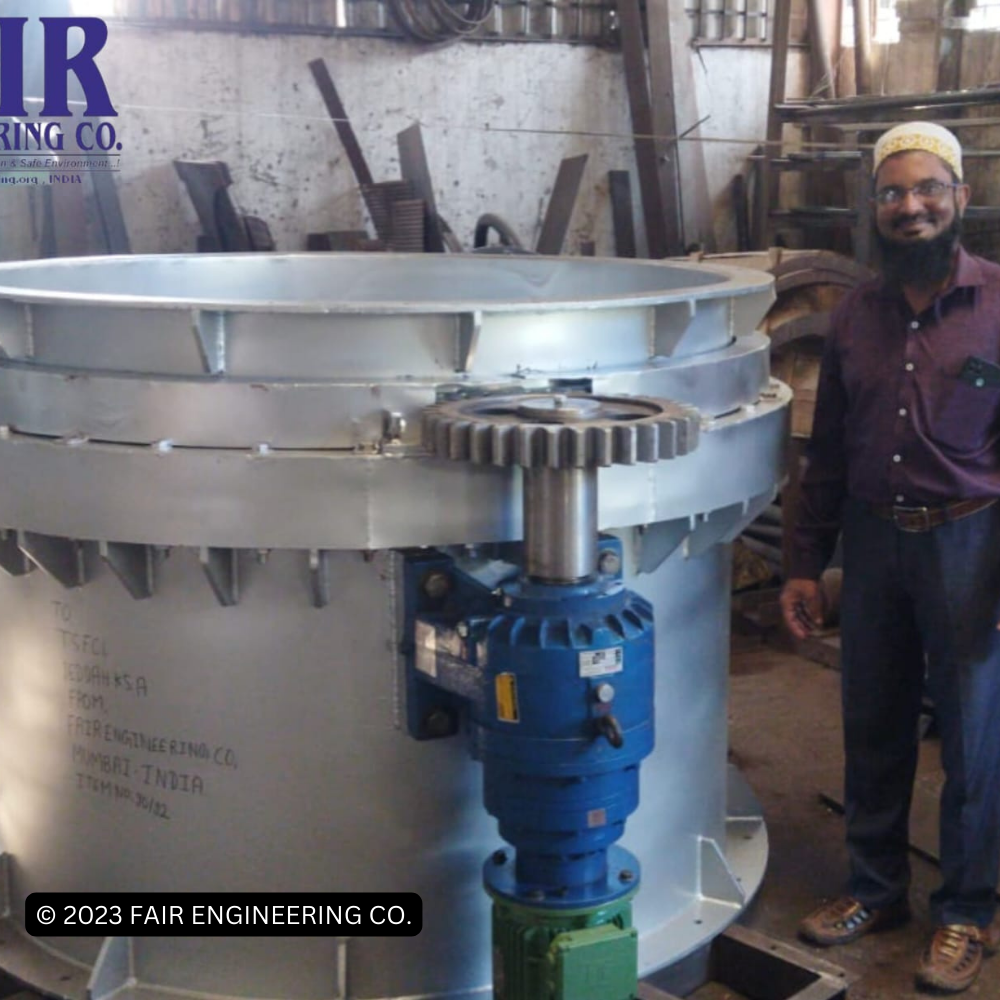
SWIVEL BEARING
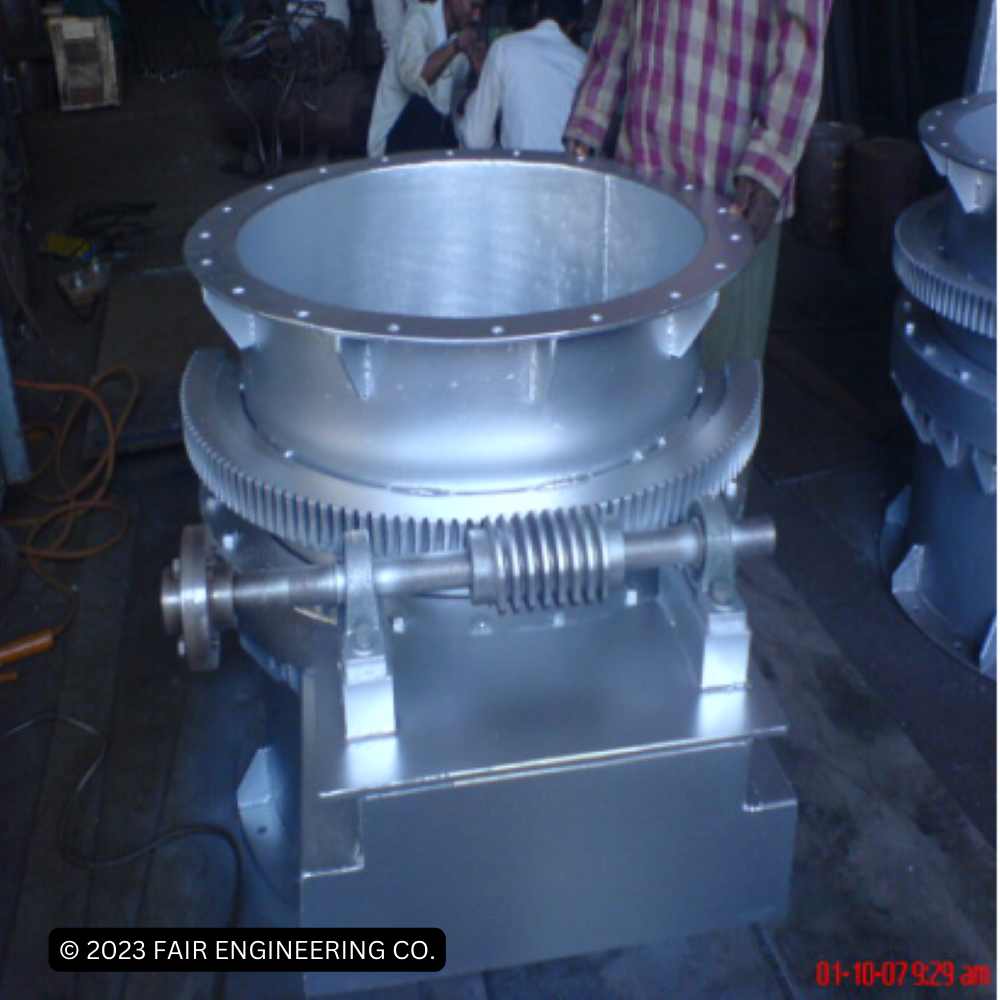
SWIVEL BEARING
FUME SUCTION HOODS - PLAIN AND WATER COOLED
Industrial activities often release hazardous fumes, vapours, and dust into the air. To prevent air pollution and protect workers from exposure to hazardous materials, many industrial facilities make use of fume suction hoods. These hoods capture fumes, vapours, dust particles and transfer them through ducts to a bag house system for air filtration process.
The most common types of hoods are canopy hoods, water-cooled hoods, and side draft hoods. Each type of hood is used for different purposes and has unique advantages and drawbacks.
Canopy Hoods
Canopy hoods are the most commonly used type of fume extraction systems. They are typically installed directly above a work area and have an extended hood which reaches over the work area. This type of hood does not hinder the workplace and provides easy access to workers near the steel melting furnace.
Canopy hoods used to capture fumes and dust particles released at high speeds or in large volumes, such as in induction furnaces. In addition, they are relatively inexpensive and easy to install.
Water-Cooled Hoods
Water-cooled hoods are a type of fume extraction system used to capture and remove fumes, vapours, and dust particles released from high-temperature processes such as AOD and EAF furnaces. This type of hood is typically installed above a furnace, or other high-temperature equipment. This type of hood is made from 5mm THK MS double walled plate or ERW pipes. There is a continuous flow of cold water helps to keep the hood material cool . To provide additional heat protection the hood is covered with layer of silica sand from inside. In addition, they are relatively easy to install and maintain. The main disadvantage of water-cooled hoods is that they are expensive to purchase and install.
Side Draft Hoods
Side draft hoods are an effective type of fume extraction system used to capture and remove fumes, vapours, and dust particles released from steel melting processes that are conducted at low temperatures such as induction furnaces. This type of hood is typically installed near the process area and has high suction velocity, also a booster axial fan to such out all fumes can be installed within channelise the fumes inside the ducts for cleaning. A typical example photograph is provided in our products list on this website.
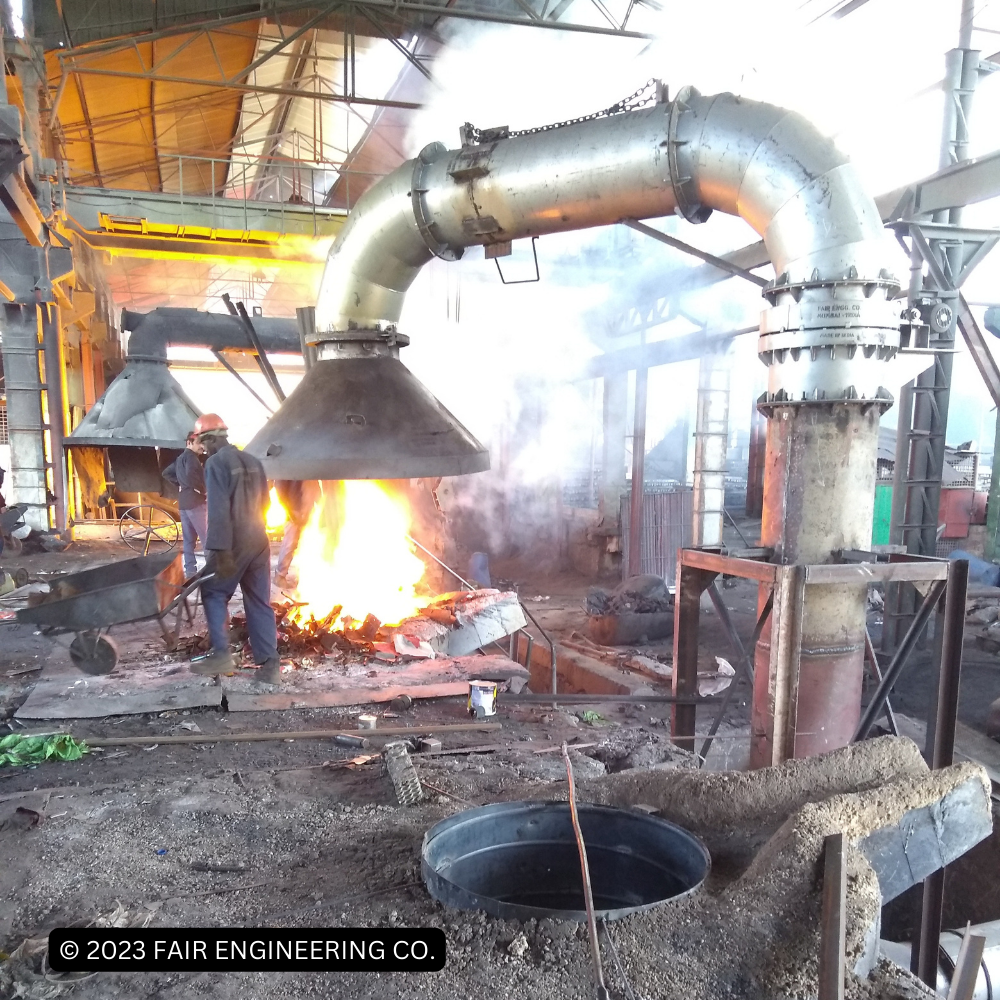
CANOPY HOODS

CANOPY HOODS
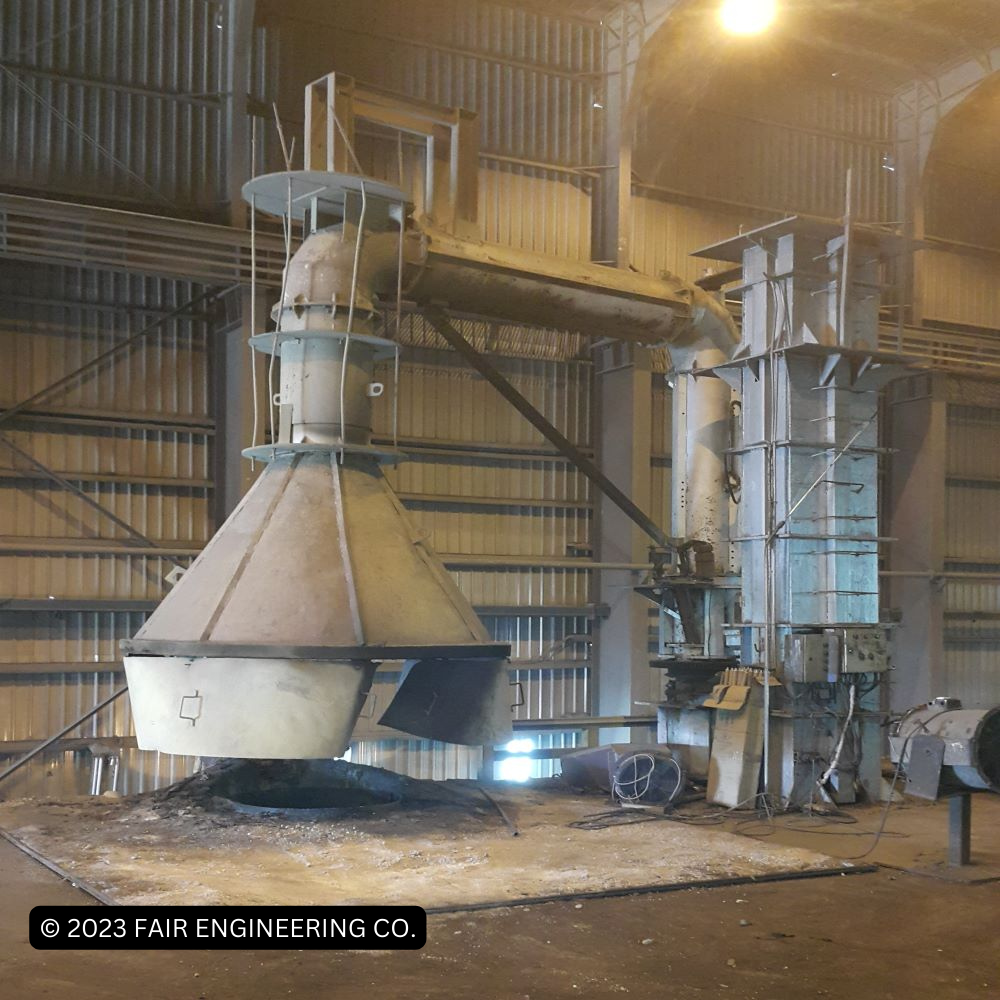
CANOPY HOODS
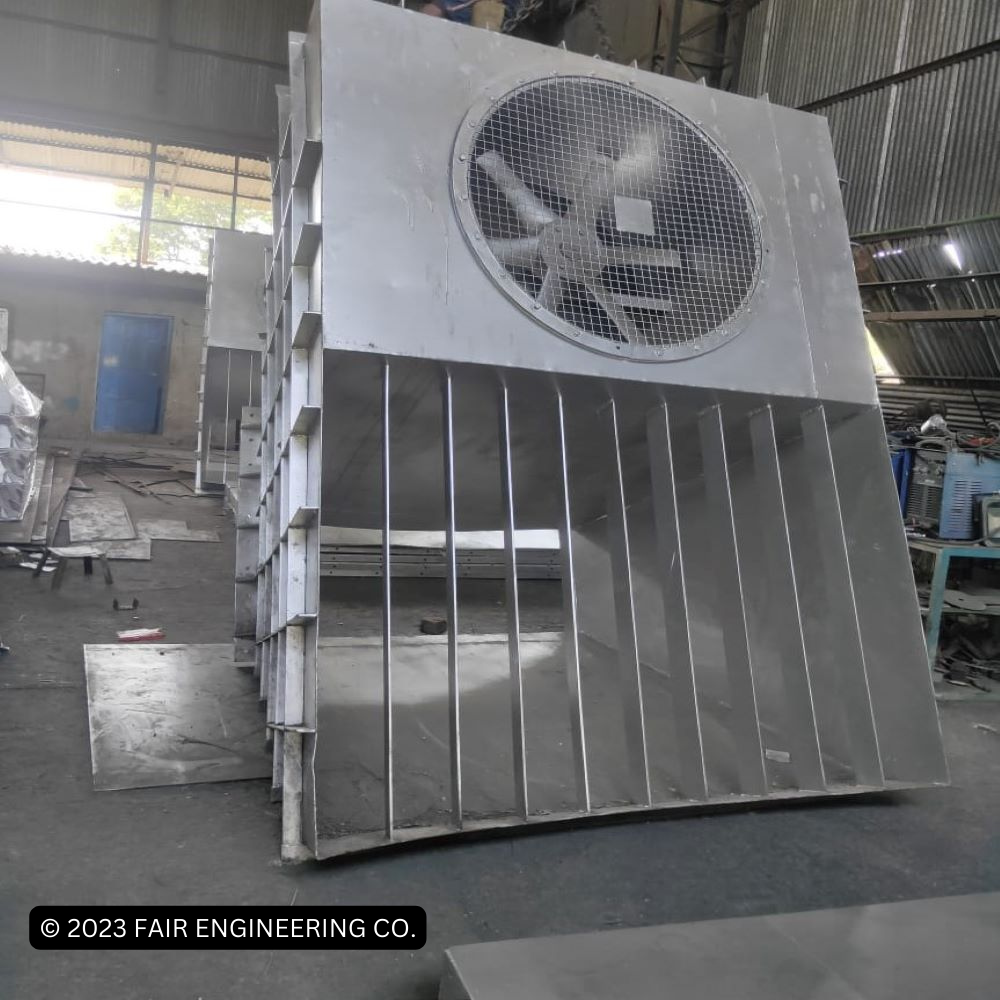
SIDE DRAFT HOOD
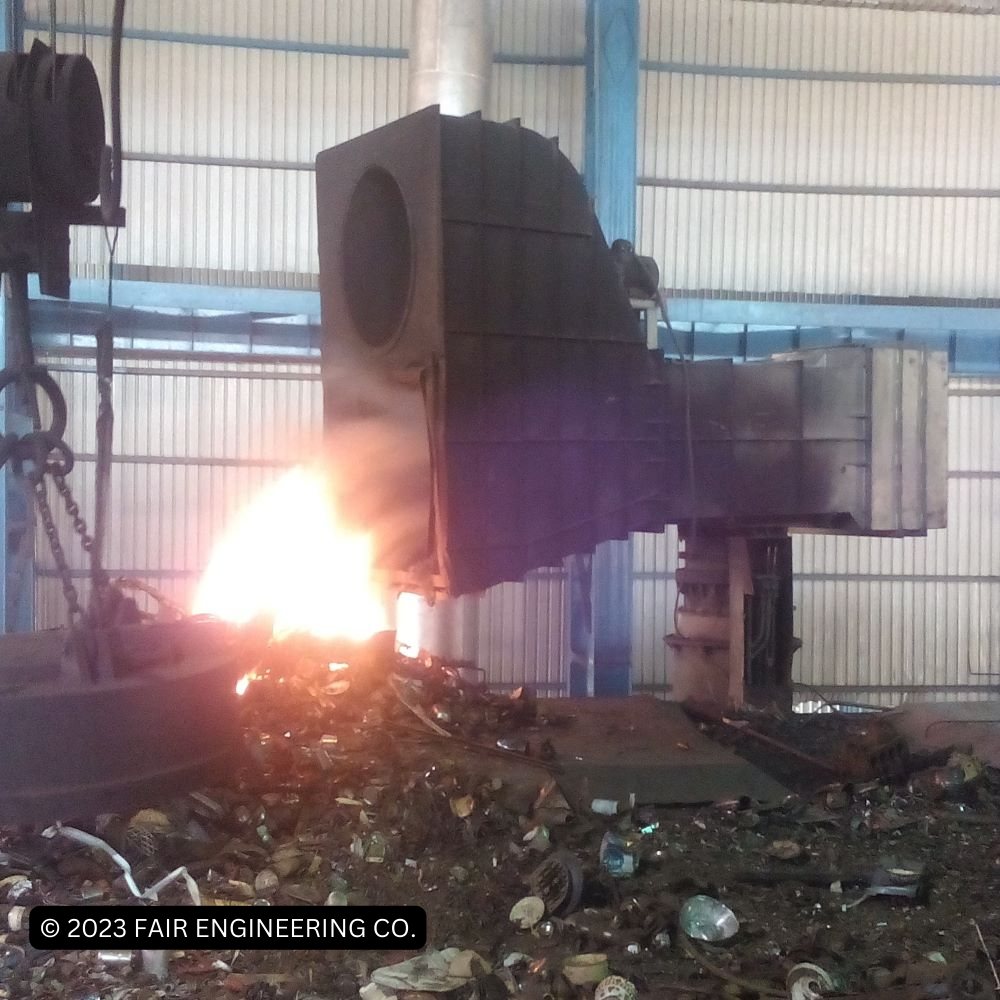
SIDE DRAFT HOOD
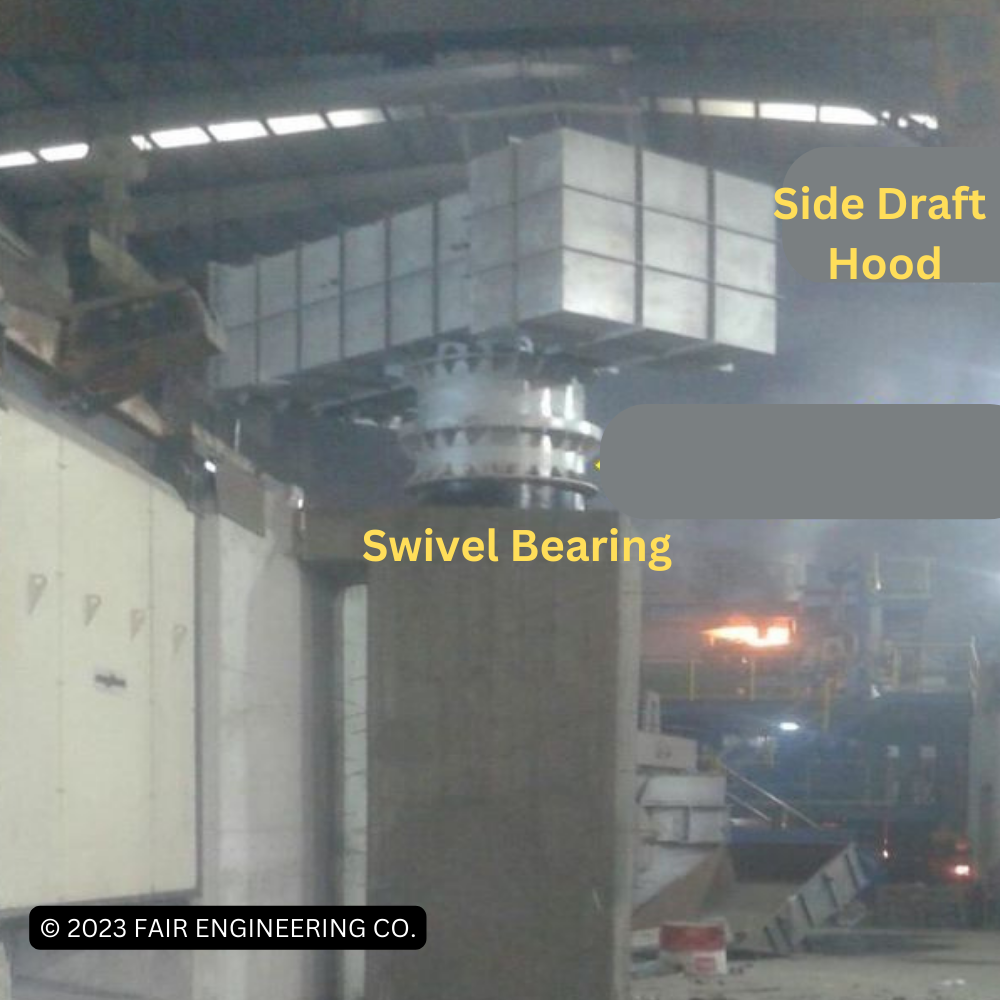
SIDE DRAFT HOOD
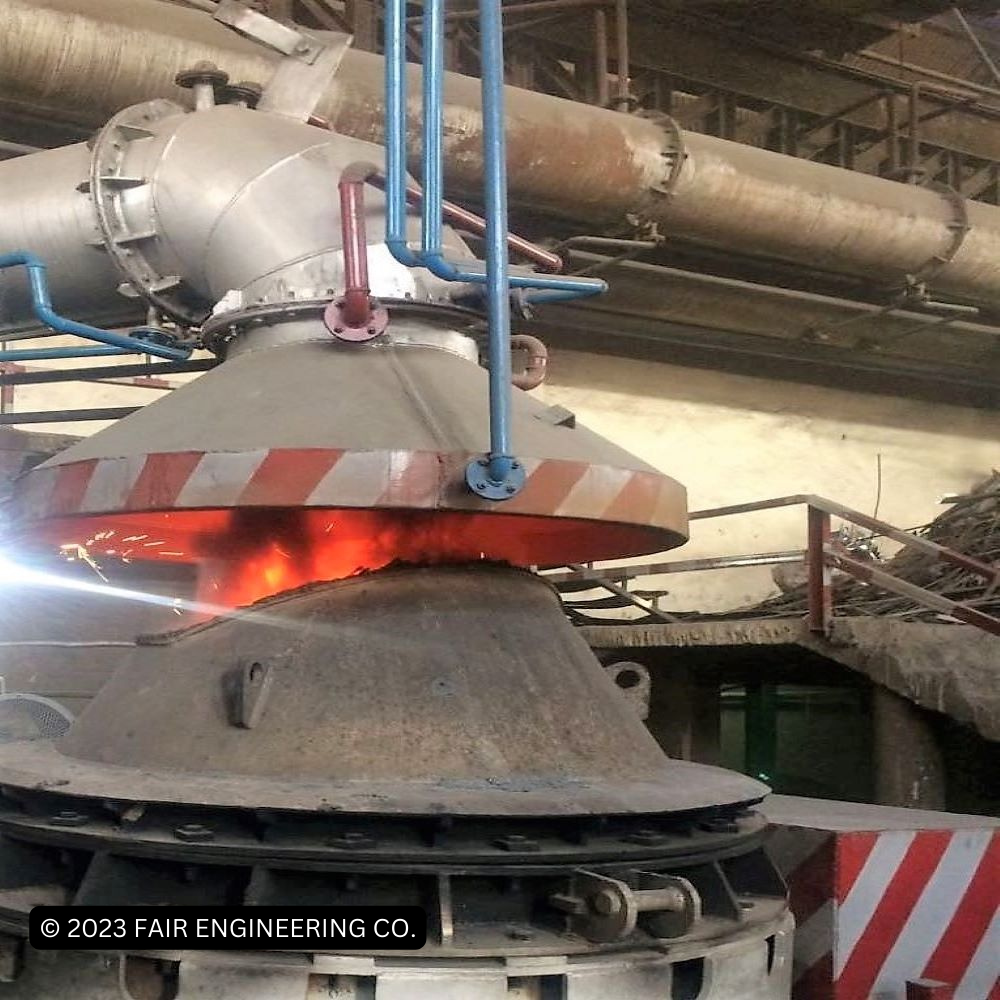
WATER COOLED HOOD
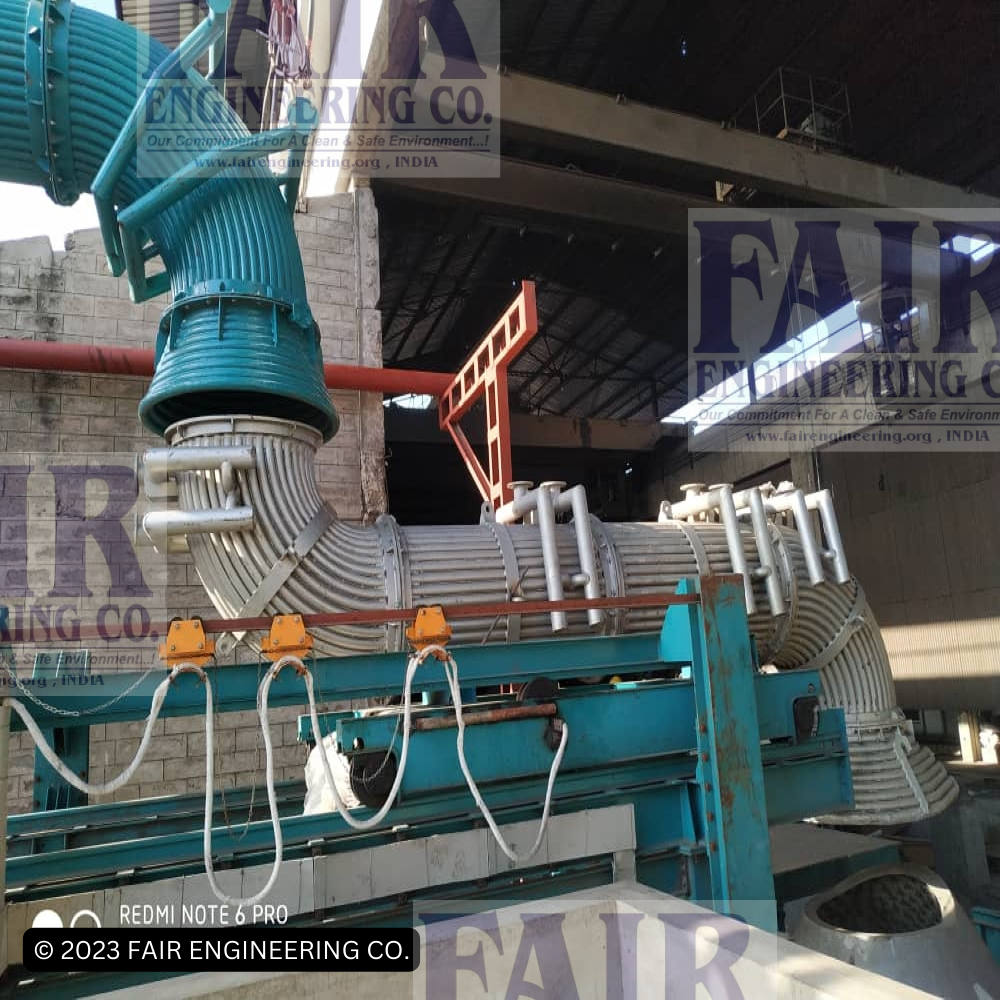
WATER COOLED HOOD

WATER COOLED HOOD